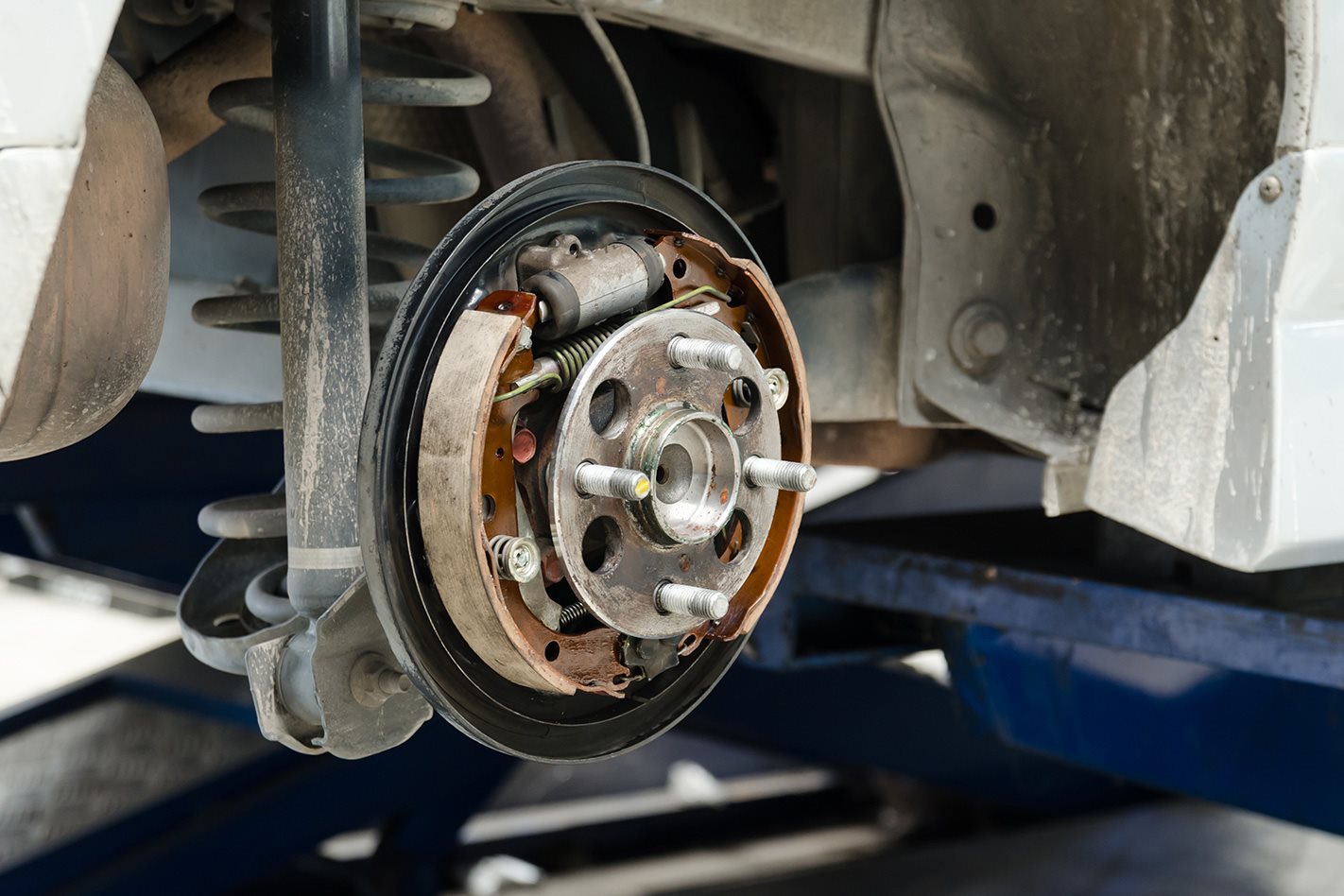
It goes without saying just how important a vehicle’s brakes are, and it doesn’t take a vivid imagination to consider the consequences of failure. Yet little thought is given for the vital systems each time you press the stop pedal.
Here’s what is going on when you lift off the throttle and ask your car to slow down via the pedal on the left.
THE BASIC BRAKING PRINCIPLE
In the simplest terms, a conventional braking system converts the kinetic energy of your moving vehicle into heat energy through friction. If the heat energy generated exceeds the energy making the car move, it will slow down.
In a little more detail – when you press the brake pedal, hydraulic pressure is fed to brake assemblies at each wheel through metal brake lines. At each corner, the pressure generated by your foot forces a lining surface that is fixed to the suspension, against the friction surface which turns with the wheel.
PROBLEMS
The accumulated heat needs to be dissipated to the surrounding air. If it isn’t, the friction surface will continue to increase in temperature until it starts to ‘fade’ – the point at which the material (commonly cast iron) cannot absorb any more energy from friction.
Fade can be caused by frequent heavy braking such as descending a steep hill or driving hard, while atmospheric conditions such as high ambient air temperatures can impede brake cooling, increasing the potential. The driver perceives fade as reduced brake effectiveness as the friction material reaches its maximum temperature.
Vapour lock is another symptom of excessive brake temperatures and is caused by the hydraulic fluid that forces the friction surfaces together actually boiling. As the liquid turns to a vapour it becomes compressible and the brake pedal starts to feel spongy, but in the worst cases the pedal can have no effect at all.
Incorrect brake fluid DOT rating or poor maintenance increases the likelihood of vapour lock by allowing atmospheric moisture to be absorbed by the fluid, lowering its boiling point. As always, the key is a good maintenance regime and getting your brake system checked as often as the manufacturer recommends.
BRAKE TYPES
For the most common car braking system, a disc provides the friction surface that turns with the wheel, while a caliper squeezes the rotor with the friction liner, or pads, to generate the friction and slow the wheel.
Drum brakes are less frequent on passenger vehicles – they’re mainly still used on cheap city hatchbacks – but are common on many commercial vehicles where they provide better braking for carrying heavy loads. In this case, a drum forms the friction surface while a pair of semicircular shoes, housed inside the drum, are forced outwards and onto the internal surface by a hydraulic cylinder.
Disc brakes are far more efficient at dissipating heat in high demand applications and are generally lighter which reduces unsprung weight for more favourable handling characteristics, but are more expensive. Drum brakes are a cheaper option but not as efficient in higher performance applications, limiting their use to more modest-performance vehicles.
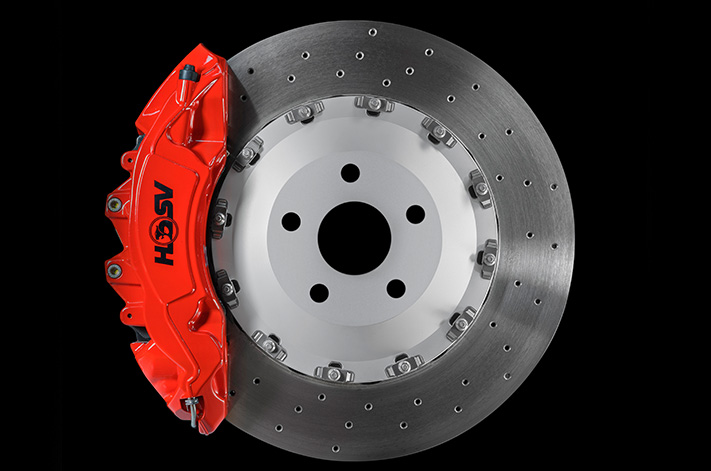
With the advent of hybrid and electric vehicles, conventional braking as we know it took a quantum leap called regenerative braking. Regardless of the type of system, friction braking is a total loss process in that it wasting kinetic energy. However, EVs and hybrids can recycle that energy as electricity and feed it back into the storage batteries.
When the brake is pressed, instead of hydraulic pressure forcing friction surfaces together, regenerative brakes use the electric drive motor to generate electricity from the forward motion of the vehicle. When a generator or alternator is asked to produce electricity, it responds with an exponential resistance that is used to slow the vehicle.
If more braking force is required, conventional friction brakes take over as the pedal is pressed harder. Advantages include increased fuel economy and extended brake component life, although some drivers find the slightly spongy brake pedal feel takes some adjusting to.
GETTING EXOTIC
In the most extreme high-performance applications the basic disc systems fitted to many passenger vehicles cannot cope with the higher stress of track and fast road driving. But more exotic materials and technology can.
Conventional discs can be cross-drilled and slotted, increasing the cooling surface area and allowing the disc to cool more rapidly when under load. They also provide somewhere for water to escape for improved performance in wet conditions.
Traditional single-piece iron discs can swap out for composite rotors that retain the iron friction ring for high heat capacity, but use a lighter aluminium hub that has better heat dissipation qualities. The composite disc is also lighter than a pure cast iron component.
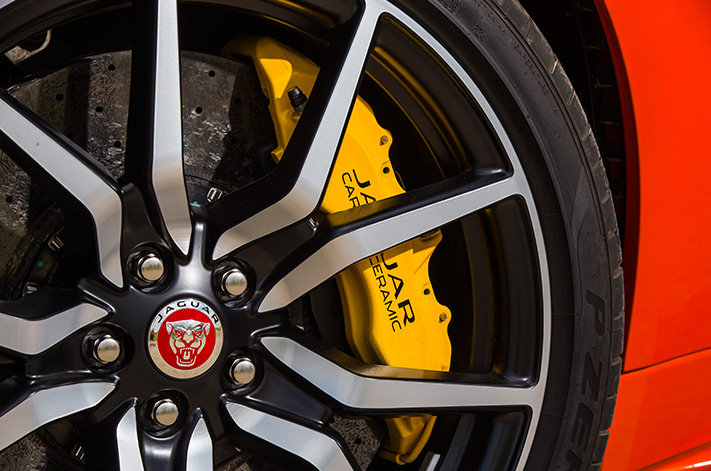
Beyond that, some manufacturers offer carbon-ceramic disc brake systems that use a rotor not made of metal, but of a sophisticated blend of carbon and ceramic materials. These discs possess extreme temperature tolerance but can also dissipate heat much faster than metal for prolonged stopping power under extreme conditions.
In both cases, the higher-performance discs are more expensive, especially the carbon-ceramic version, but they also have another disadvantage. Metal rotor thickness needs to be periodically measured to determine when they have worn to their minimum thickness and need to be replaced, but the wear of ultra-hard carbon-ceramic discs is almost undetectable.
Instead, the material becomes lighter as the resin holding the special materials together vapourises. The discs must be removed, and weighed, to determine when replacement is necessary.
GET A GRIP
Calipers can also upgrade for added braking performance. While basic disc brakes use a single-piston caliper that ‘floats’ as it pinches the disc, fixed position versions using multiple pistons increase clamping pressure and surface area with larger pads to generate heat faster and provide more braking force.
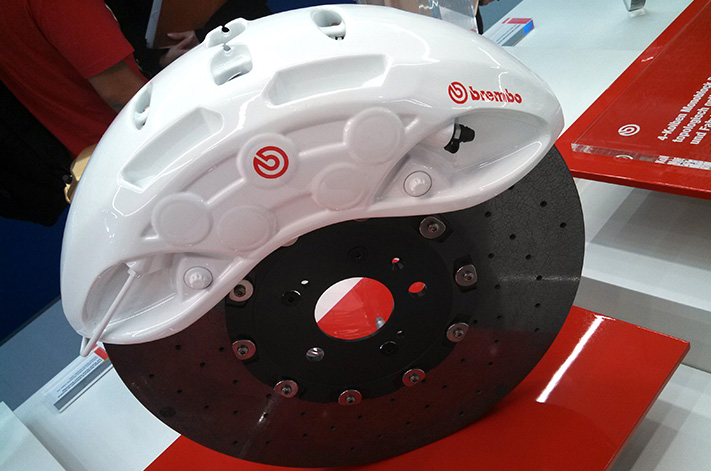
One of the world’s leading high-performance brake component brands, Brembo, offers a caliper with 10 pistons for the ultimate in clamping force.
Alloy high-performance calipers are also lighter than the equivalent cast iron version, offering more weight-saving potential.