With an all-new V6 turbo engine bolted to plug-in hybrid powertrain, ground-up aluminium and carbon fibre monocoque design, and a revolutionary ethernet network, the Artura is arguably the most daring car to ever emerge from McLaren’s Woking technology centre.
But its technical accolades are more intrinsically woven into the aesthetics than most would realise. McLaren chief designer Joao Dias reveals some of the Artura’s secrets that hide behind a super-formed aluminium skin.
What appears to be a top-exit exhaust a-la 600LT is, in fact, a heat chimney to channel superheated air away from the pair of turbos nestled in the 120-degree V6’s hot-vee, and the hot air can be seen by the driver in the rear view mirror as it rises from the duct.
Dias explains that a huge amount of effort was put into extracting heat from the engine bay which measured up to 800 degrees in testing.
C-pillar flying buttresses increase airflow into the engine bay, while the tail light design was slimmed to maximise the amount of hot air escaping through the full-width rear aluminium mesh. Heat challenges also prevented engine bay illumination found in the 720S – “Engineering told us everything would melt,” said Dias.
The Artura’s rear-mounted radiators are fed air via two large vents clearly visible behind the doors not hidden inside the door like the 720S design.
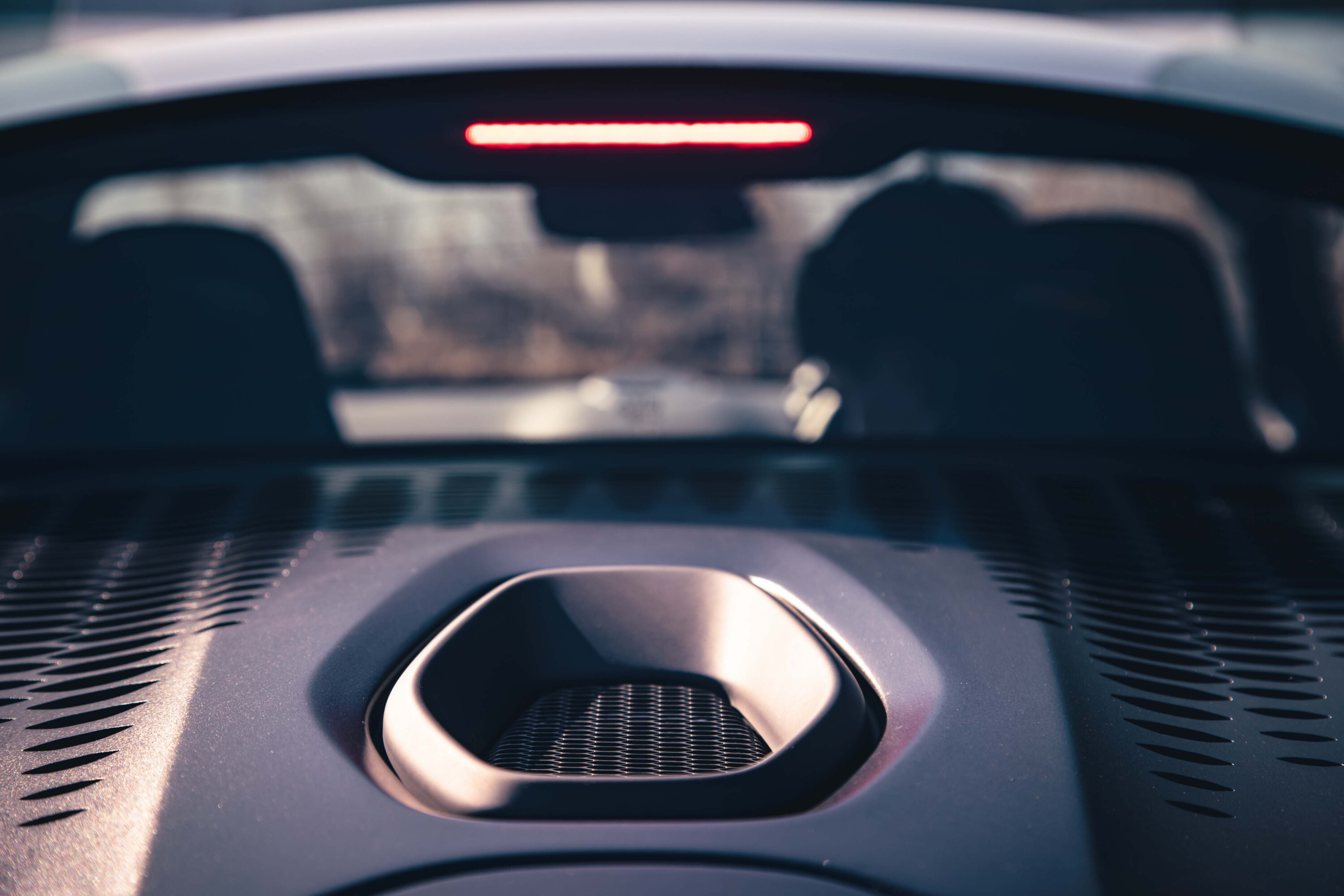
This, says Dias, was to reduce weight and complexity with the panel instructed using a single super-formed aluminium sheet compared to the 720S door which was built from 11 separate panels.
“We didn’t want a Senna-like aperture. The Artura had to give a similar level of drama but with a more simplistic execution,” he explained.
McLaren’s Woking manufacturing centre is known for its lack of automation and silence but there is one machine that was necessary to make the Artura possible. Its roof is the largest body panel and is impossible to install using human power alone so the ‘aided tool’ was added to the production line.
Dias said that introducing the first machine to the manufacturing centre was a significant decision but the company is not governed by principles if they stand in the way of progress.
“If the theme is going to be more expensive to deliver but everyone loves it, the business is going to adapt the process and budget to deliver that. This is one example.”
Maintaining a short wheelbase for packaging, proportions and handling was a significant challenge, but the engineering team worked with the designers and succeeded in fitting both the V6 engine and hybrid batteries inside the new carbon fibre passenger cell. Dias says a longer wheelbase would be acceptable for a larger McLaren but not for the “baby” Artura.
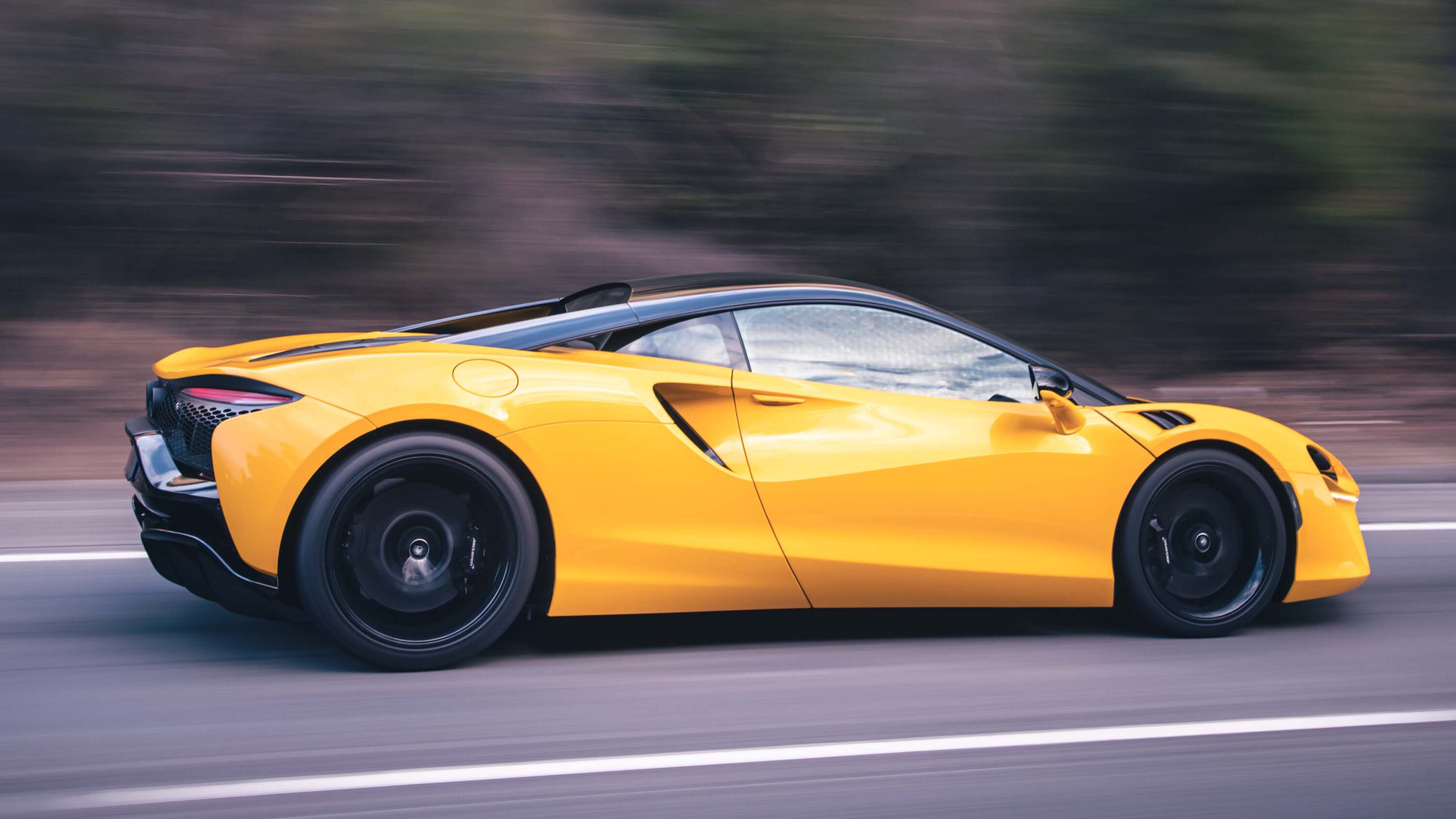
“The challenge was always to keep the wheelbase as short as possible,” he said. “If you had a V8 engine with the batteries, this wheelbase would have to grow 60mm.
“For the successor of the 720 which is a bigger car, maybe it could be possible, but for this, it was the limit.”
Dias’s biggest challenge was actually one of the Artura’s smallest details, and finalising a design for the door handles which looked right but didn’t upset airflow into the radiators took months of back and forth.
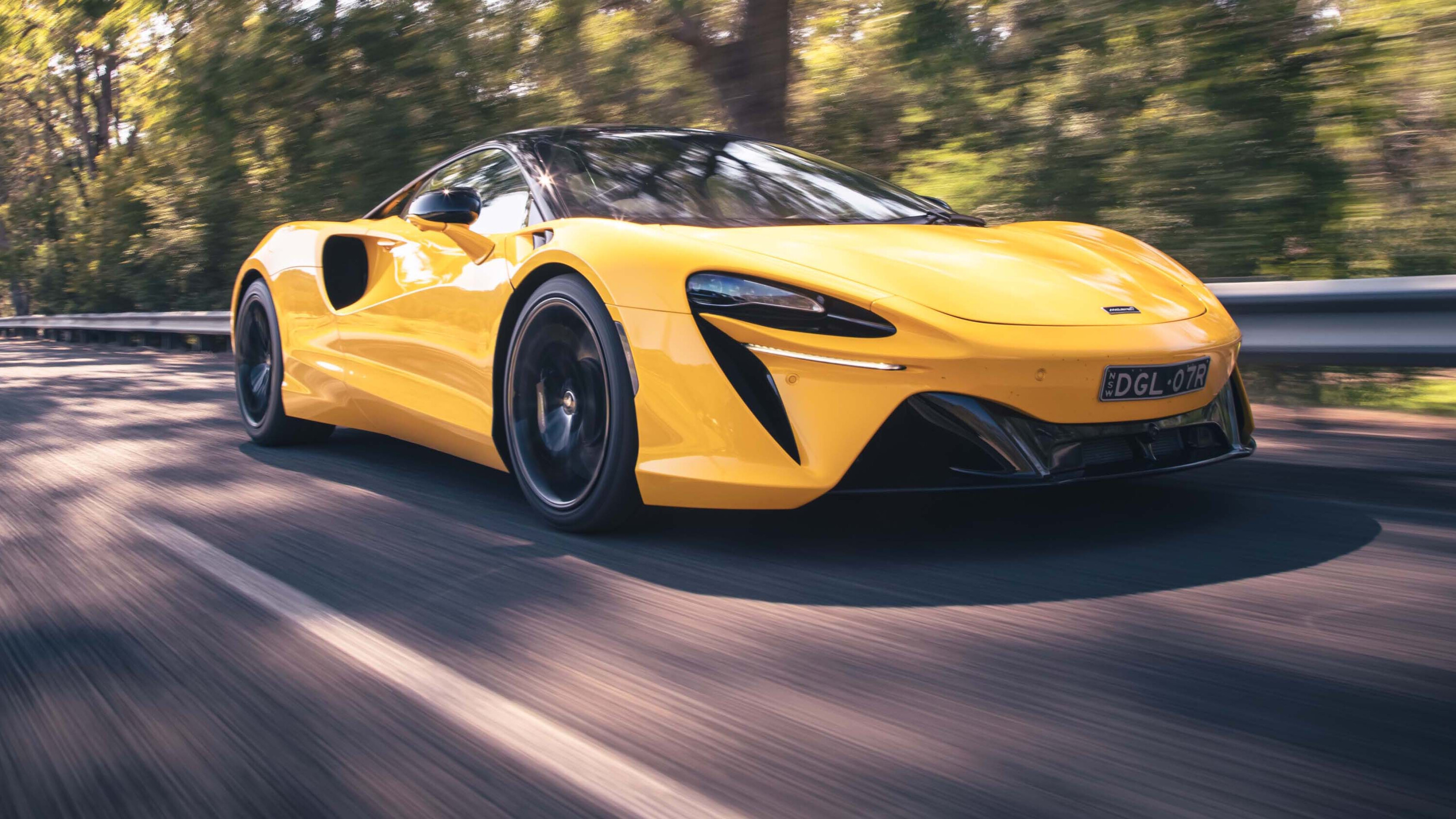
“If you embrace the technical, your creativity doesn’t stop. If you see the technical as an obstacle, your creativity will always be affected”
“Engineers wanted to cut a hole in the surface and put a plastic door handle in there. I said, this is not going to happen. I’m not joking – we spent three months on this.”In the end, inspiration came from, of all things, a common household item.
“At home I had a shoe cupboard and to open the door was this very thin aluminium part with a lip.I told the guys from ergonomics the only thing we need is just enough grip to pull the door.”
“If you embrace the technical, your creativity doesn’t stop. If you see the technical as an obstacle, your creativity will always be affected”
We recommend
-
Reviews
2022 McLaren Artura review: International first drive
McLaren Automotive's second all-new car in its 12-year history is all grown up, but is that what we want from a plug-in hybrid supercar?
-
Features
The Artura is McLaren’s most important car since the F1
A decade of knowledge is distilled beneath the McLaren Artura’s sheet metal ... welcome to Woking’s V6 hybrid era
-
News
Revealed! This is the McLaren Artura hybrid supercar
Downsized, hybridised... but with performance into the next dimension