
Snapshot
- New tech allows Bugatti to create ultra-thin, uber-stiff components without a brittle nature
- 3D-printed titanium brake calipers and suspension components can be put into production
- Mixed ceramic and titanium composite material also being developed
The Bugatti Bolide is what happens when the engineers behind the Chiron hypercar look at their own creation and think “that’s a bit too slow for us”. Looking like an LMP1 car that spent too much time hanging out with Arnold Schwarzenegger, the Bolide was a no-holds-barred ‘what if’ concept that allowed Bugatti to push its engineering process to the limit.
We aren’t here to talk about the Bolide in totality though, it’s several, very small, components underneath the dramatic skin that have us at MOTOR HQ geeking out.

Begin peeling away the exterior panels and very quickly you’ll discover several core pieces of the Bolide’s race-spec pushrod-design suspension – including the brackets and springs – are constructed not from aluminium, but of 3D-printed titanium. However, it is the pushrods themselves that are most impressive. Bugatti is so proud of its design that it has patented the internal structure. Put one on a scale and it’d register just 100 grams, but it is capable of taking 3.5 tonnes of punishment thanks to a construction process known as selective laser sintering.
Each pushrod starts its life as a pile of Ti6AI4V titanium powder, with the printing process, which engineers would prefer you call additive manufacturing, being incredibly time consuming. While the 3D printer your geeky cousin uses lays down a single solid stream of liquid material that then solidifies into the final product, Bugatti uses the method called selective laser sintering. Thousands of layers of the powder are put down progressively, each being melted by a laser, essentially welding the final product into a single piece like a reverse-billet. After being ‘printed’ each part is then furnace-treated at 700 degrees Celsius, before being ‘cooled’ to 100 degrees Celsius to boost the dimensional stability and remove residual stress.

Using selective laser sintering, Bugatti is able to print titanium with an accuracy of 0.1mm – or about the same thickness as the paper this story is printed on. The suspension components have a hollow interior, and incredibly thin walls (down to 0.4mm in some places), while also remaining incredibly strong. This is thanks to the organic, bone-like design of the components. Taking inspiration from organic structures, Bugatti was able to strike a balance between weight and strength.
Bugatti didn’t stop at the suspension. The mounting bracket for the Bolide’s steering column includes an integrated dashboard support and is 3D printed, along with the steering column’s support collar and the interior air vents – all with a uniform wall thickness of 0.5 mm. Other printed components include the turbo-fan wheel covers, plus front- and rear-wing mounts. For the front splitter, a bracket was created with a wall thickness of 0.7mm that allows it to be adjustable with three different height settings, while also being rated for 800kg of downforce and weighing just half a kilo.

While still relatively new, 3D printing processes have been undergoing intense scrutiny by multiple car companies for several years, with an aim to improving the vehicle manufacturing process (and boosting performance along the way). Fiat-Chrysler announced a partnership last year with Fraunhofer, resulting in an experimental component that integrated parts of the wheel hub with the brake calliper. The resulting single-piece prototype does a job previously completed by 12 individual parts, while weighing 36 per cent less. Meanwhile, Porsche has used the technology to produce power-boosting pistons for the GT2 RS, while Bugatti developed a powerful new brake calliper design for its warp-speed hypercars (see breakouts, right).
Head of new technologies at Bugatti, Frank Götzke, says the 3D printed titanium components have a tensile strength of 1250 N/mm2, with the heat treatment process resulting in a high fracture strain of at least 19 per cent. Don’t speak fluent engineer? The layman’s translation is Bugatti has created ultra-thin, uber-stiff components without a brittle nature.
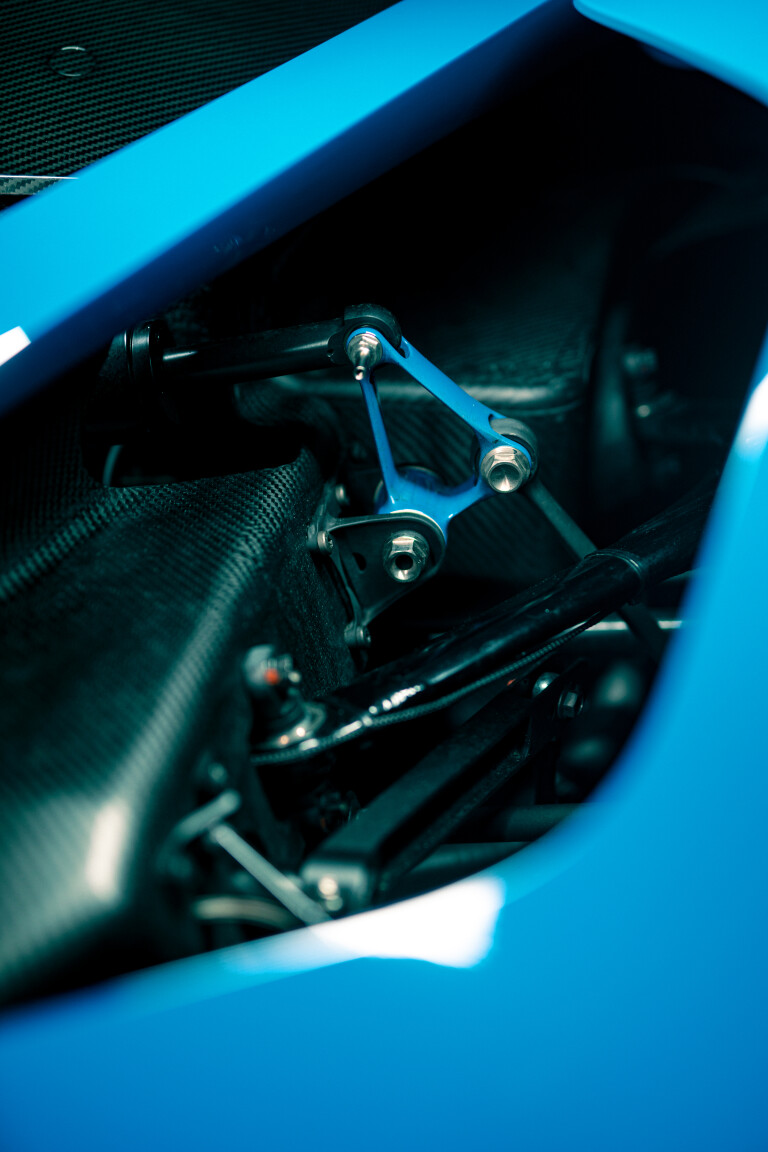
While Bugatti’s design is currently at the bleeding edge of printing technology around the world, it’s thought that continued development will result in savings for car companies.
“The overall focus is on the reduction of manufacturing costs, for example, by significantly increasing production speed,” explains Ruben Meuth, Head of Business Development at experimental parts manufacturer Fraunhofer IAPT
Your regular vehicle manufacturer can’t match the bottomless pockets of a hypercar company like Bugatti, but expect these science-fiction technologies to become more democratised and commonplace sooner, rather than later. This will result in less unsprung mass, increased dynamic capability, and more enjoyable drivers’ cars all round.
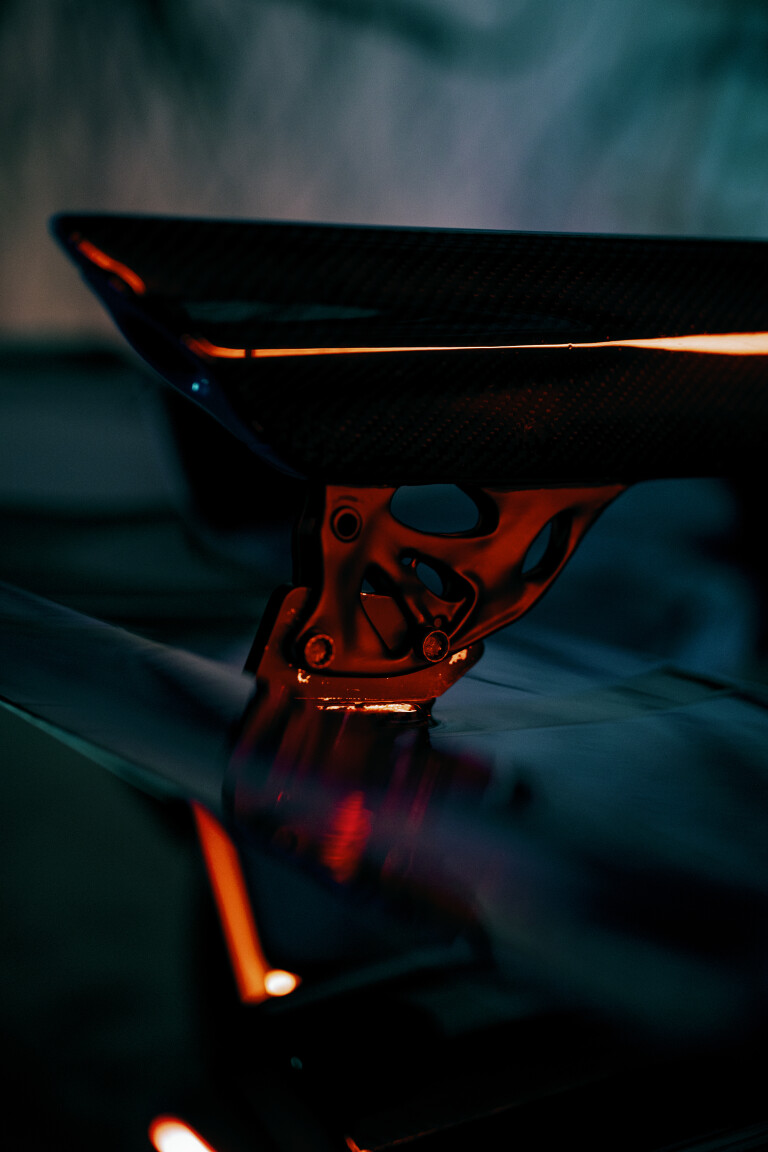
THE MAN BEHIND THE PRINTER
Bugatti’s edge in this area is thanks to Henrik Hoppe, who leads the manufacturer’s selective laser melting projects. As a doctoral student, Hoppe wrote his master’s thesis on a calculation methodology for creating 3D printed titanium brake calipers. Expect any hypothetical head-hunting from rival manufacturers to be headline news.
BIGGER AND BETTER
Bugatti already had the most powerful braking system ever fitted to a road car when it released the Chiron, but in 2018 the firm went ever bigger by developing a monobloc caliper design produced using additive manufacturing. The French manufacturer claims the eight-piston caliper it created in was the largest functional car part ever 3D printed with titanium. Measuring in at 41cm long, 21cm wide, and 13.6cm high, the titanium unit weighed 2.9kg, compared to the then-aluminium production equivalents 4.9kg.
PRINTING POWER
A Porsche technical study in 2020 resulted in the company 3D printing a set of pistons for the 911 GT2 RS, boosting power from 515kW to 537kW. The pistons are 10 per cent lighter than a conventional equivalent, while incorporating a new cooling channel to lower ring zone temperatures by up to 20 degrees Celsius. Along with the 4 per cent power bump, the units underwent a 200-hour endurance run on an engine dynameter. Porsche’s engineers teamed up with three separate companies to help tackle the engineering challenge.
MIXING CERAMICS
Bugatti has created a mixed ceramic and titanium material that is capable of being 3D printed, using it on exhaust systems. It claims the hybrid product is a “significantly less effective heat conductor than titanium” allowing it to be used in the construction of thermal shields.

COMMENTS