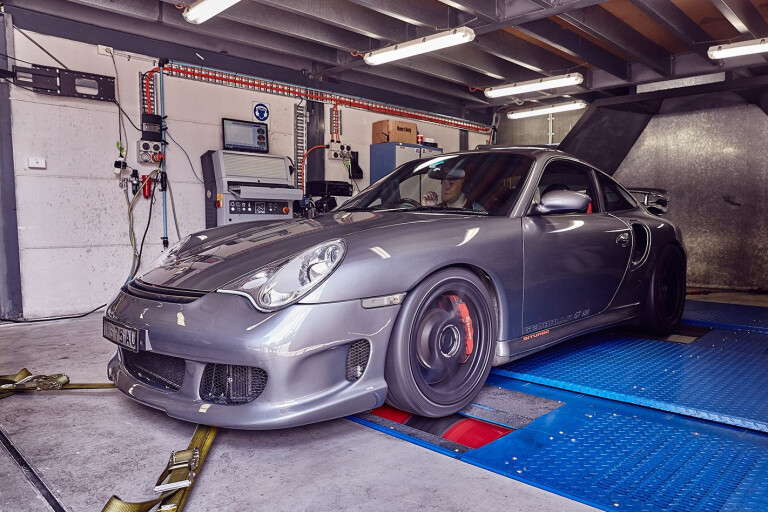
THE history books rightly record the birth of the dynamometer in 1719, more than 150 years before the car.
You see, dyno doesn’t necessarily mean rolling road, though the world’s first dyno – invented by ‘Honest’ George Graham of London and adapted by French-born Brit John Desaguliers – did measure horses and pulling power.
The early dyno was a crude device that provided a means of comparing linear force, such as that provided by a horse. These mechanical machines didn’t put a number on the pony’s power, so weren’t much chop for bragging rights at the mead hall, but helped 18th century military generals select their strongest steeds.
It wasn’t until 1928, however, that Germany’s Carl Schenck Eisengiesserei and Waagenfabrik devised a dynamometer that resembled what can be found in today’s workshops.
These ‘chassis’ dynos are the most common in the aftermarket – the amount of power and torque at a car’s wheels (or hubs) is useful because it tells tuners how much the engine has to push the car, less any driveline losses – while automotive engineering departments use ‘engine’ dynos in their development programs.
Inertia dynos, water-brake (or hydraulic) dynos, and electric (or eddy-current) dynos are the three main types of chassis dyno. An inertia dyno can only do full-throttle acceleration runs, while hydraulic and electric dynos can simulate road conditions and have the potential to deliver greater accuracy.
‘Roller’ and ‘hub’ dynos are common, the latter usually regarded as more precise because it removes the room for inconsistencies caused by tyre growth and slip by bolting directly to the car’s hubs.
But the point of a dyno ‘test’ is how the pre- and post-modification figures compare and how they relate to on-road performance, not necessarily how precise they are. Speaking of accuracy, most modifiers know that not all dynos measure equally, whether through operator error or a tricking of the dyno’s various sensors. Those who like to boast could probably even tell you which workshop’s dyno is the most ‘powerful’.
However, German-car tuning outfit BWA Auto in Sydney’s Seven Hills isn’t in the pissing contest, instead claiming that its advanced MAHA all-wheel-drive dyno – the only one in the country – can read flywheel power to within two per cent.
Uniquely, the German-developed roller dyno has the capability to electrically spin the non-driven front or rear wheels, simulating road conditions to trick the ECU, for measuring the likes of hybrids and PDK Porsches.
DYNOSTY
Airflow, barometric pressure, temperature, and torque calibration apply when testing a dyno’s accuracy. Compared with an engine dyno, there are also drivetrain losses, inertia, brake drag, vehicle tie-down tension, and tyre slip.
GEAR UP
Use higher gears to minimise drivetrain friction and inertial losses. Lower gears multiply torque and can increase tyre slip. Using a higher gear lets engine revs build more slowly.
CRACKING THE CODE
Is there anything that can’t be tuned? Well, while modern ECUs can be more difficult to crack than their predecessors, there is still no such thing as anti-tuning software.
TUNED IN
The benefits of a reprogrammed ECU can be immense, especially on a turbo or clutch-controlled supercharger car, so get on the dyno before you bolt on that bigger turbo.
LOST POWER
Armed with an at-the-wheels dyno figure, many punters would like to know what percentage of engine power is lost in the drivetrain. The answer? It all depends on the drivetrain.
PRECISE v SIMPLE
On an inertia dyno, the amount of time it takes the car to accelerate a heavy drum to a given speed corresponds directly to the power output at the wheels. An inertia dyno is a relatively simple device that’s less costly and less prone to having its results fudged than more complex dynos.
However, it doesn’t realistically replicate road conditions, which limits accuracy. Electric current provides the power absorption in an eddy-current dyno, rather than a fluid (hydraulic dyno), which brings the ability to simulate real road loads, making eddy-current dynos ideal for precise ECU calibration.
COMMENTS