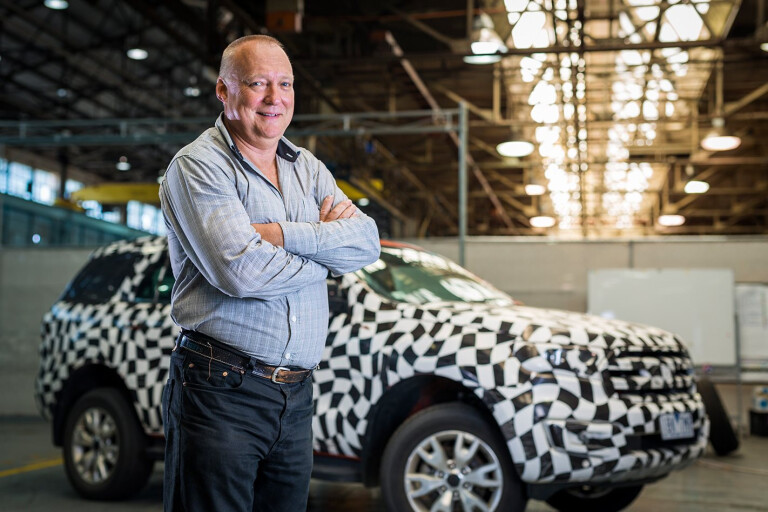
Stretching to Lycra was a defining moment for Ford camouflage expert Neil Trickey.
First published in the March 2016 issue of Wheels magazine, Australia’s most experienced and most trusted car magazine since 1953.
IT’S a fair bet that when Neil Trickey began his apprenticeship as a fitter and turner in the small Victorian town of Maryborough, he wouldn’t have guessed he’d one day be designing slinky, body-hugging outerwear for Ford models. That’s “Ford models” as in Falcon sedans and Ranger utes, not the New York fashion agency.
Trickey, 57, joined Ford Australia in 1977 and moved into the prototype shop in 2000. “It really is an interesting job,” he says. “The engineer comes to me and says, ‘I want to make this widget’. So I go off and make a prototype part that he wants as best I can, or as best we can get it made. It could be any part of the car. And we’re playing with these things three years before you guys get to see ’em.”
Trickey’s worked in many different areas of toolmaking, with a lot of experience with CAD and sheetmetal stamping. He’s also the go-to guy for prototype camouflage.
“We used to use fibreglass, vacuum-formed panels, all sorts of things,” he says. “Then there were the vinyl covers. They added a lot of weight and we discovered that they tended to hold the vehicle together. They’d test the vehicle for months and it’d be terrific, but when they took the camo off, they started finding the bumpers coming loose. It also distracted from the wind-noise and cooling.
“We moved to stretchy Lycra covers after I saw a Holden Commodore, a VE, all camouflaged, driving past me one day. I found out that a Melbourne company had developed the idea to use Lycra.
“It was quite good, because the first job – I think it was BA Ford Falcon – we’d gone through prototype build, say 50 cars, and they said there wouldn’t be any XRs in the mix. So I made all these camouflage covers off a base-model car, no spoilers or anything. The first car that came down was a GT! But the Lycra just stretched over everything. You just clip it on, it hit all the high spots and you couldn’t see anything in between. It was brilliant.”
To make the covers (they’re sometimes subbed-out to upholstery shops), Trickey starts with measurements from the previous model. “Then we lay it over the clay model – when we’re allowed to – being careful not to damage them. We also have our CAD information. But you don’t really know that it’s going to work until you drive one out onto the road.”
The prototype test team loved Lycra, too. “The old vinyl camo would stay on the cars pretty well, but every day the engineers need to take it all off to do their tests and take readings. Where the Lycra, it had a separate engine hood bag, separate bumper-grille-headlights – it’s so much easier for them.”
As keen readers will know from our News pages, the Lycra is gradually being superseded by psychedelic-patterned adhesive film.
“It’s about as quick to put on as the Lycra, it doesn’t add any weight or affect the aero at all,” Trickey says. “The only thing is, I don’t think it hides quite as well.
“Still, the managers seem to like it. They’re the guys you’ve got to impress, I suppose.”
Camo king
Ford camouflage expert Neil Trickey says there are several stages of prototype. “There’s X1, the basic concept in terms of size, seating position or whatever ... Then you go into M1, where the underbody has all got to be correct. Then it’s VP, verification prototype, where the ‘top hat’ is about 80 percent there. By then, you’d want pretty good camo.”
COMMENTS