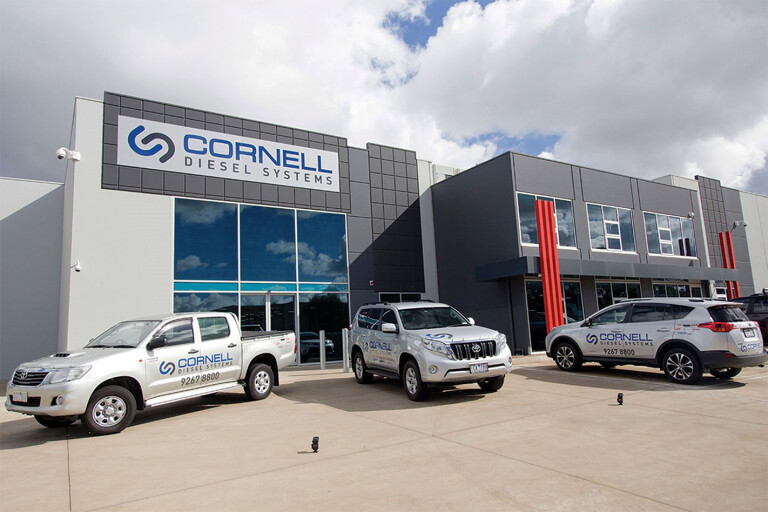
In August 2016, Cornell Diesel Systems (CDS) relocated to a brand-new state-of-the-art, purpose-built facility in Sunshine West, Victoria. The site is huge – measuring approximately 4000m² – and is four times larger than the previous site, reflecting the growth in demand for a specialist diesel service.
Moving into bigger premises allowed CDS to increase its workload by accommodating more mechanics, which enabled CDS to broaden the scope of work it performs. Instead of focusing solely on diesel pump and injector removal and replacement, it has moved into engine replacements and repairs, as well as general repairs such as servicing, clutch replacements and brakes. It has also allowed the company the freedom to take up work on large vehicles.
The bigger premises allowed CDS to install a 4WD dyno, which has helped grow the vehicle-performance-upgrade portion part of the business. The goal is to have the workshop full and to offer customers a state-of-the-art facility so that they feel confident and comfortable their vehicle is in the right hands.
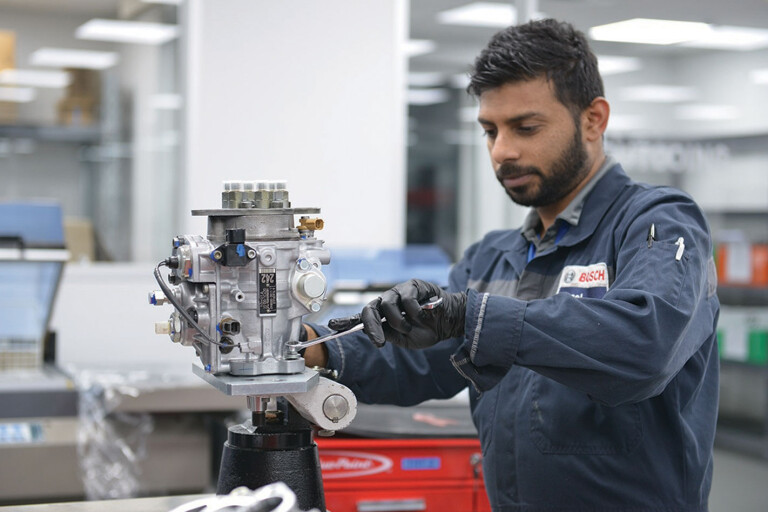
KEEPIN’ IT CLEAN
THE BUILD and test room covers approximately 500m² of floor space and was constructed as a pressurised clean room. In addition to strict temperature control, it includes HEPA and charcoal filters to maintain air quality. Controlling air quality is very important when it comes to repairing common rail pumps and injectors. All OEMs (including Denso, Bosch and Delphi) insist their pumps and injectors are assembled in a room where air quality and temperature are regulated to ensure internal parts have been measured accurately in a controlled environment, and to ensure they meet the OEM specifications, quality repairs and outcomes.
This adherence to cleanliness and controls is very high in the new premises – and for good reason, according to Anthony Grech, CDS operations manager.
“Cleanliness is very important, whether you are working on common rail components in the pump room or removing them from a vehicle in the workshop,” says Grech. “That is why CDS prides itself on the cleanliness of its premises, from the build and test room through to the workshop. Not only is it a clean and pleasant place to work in, but also a part of the requirements to be an authorised repairer.”
These requirements are at the behest of OEMs, who insist that common rail pumps and injectors are assembled in a clean room and tested in a controlled environment. Even when it comes to replacing diesel components on a vehicle, cleanliness plays an important role, as Spiros Katsoulis, CDS service manager, further explains.
“When removing common rail injectors from a vehicle, the capping and bagging of the HP fuel lines is recommended, as well as the capping of the HP common rail. General cleanliness of the work area is paramount. All of these precautions may seem over the top, but any dirt or contamination that finds its way into a diesel fuel system, whether it be mechanical or common rail, can have a detrimental effect on the performance of the diesel components or fuel system.”
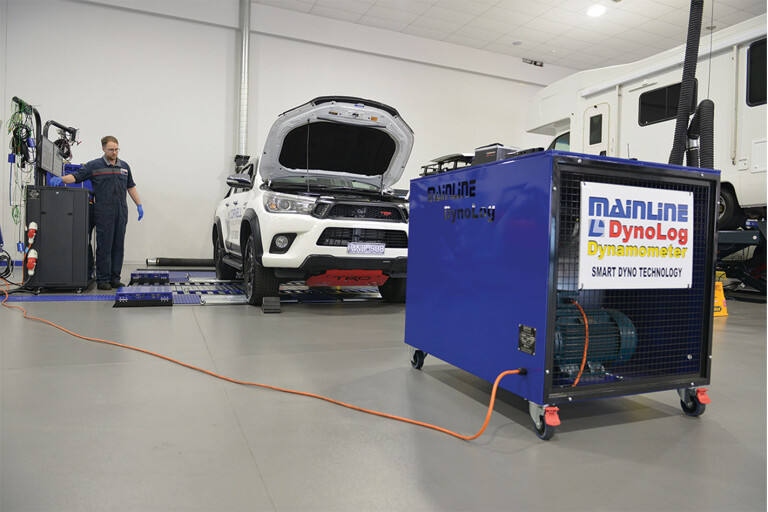
PUMPING IT UP
THE FACILITY boasts Australia’s most well-equipped pump room. The pump room is sectioned to separate various functions and ensures stringent cleanliness standards are maintained, which is essential for the service and repair of modern high-pressure diesel systems. Units are sorted and cleaned in the incoming and dismantling areas prior to being inspected and dismantled, and tools and equipment used in this area stay in this area. The pump room is equipped with a massive array of test benches, which points to CDS’s ambition to become the leader in the aftermarket diesel field.
“CDS’s goal is to be your one-stop shop for all your diesel needs, big and small,” affirms Grech. “We pride ourselves on having a large range of new and exchange products on the shelf, which in turn means the customers can get their vehicle back on the road quicker, limiting downtime. Having exchange products also means that we can offer quick turnaround times for repairs that happen in our workshop.”
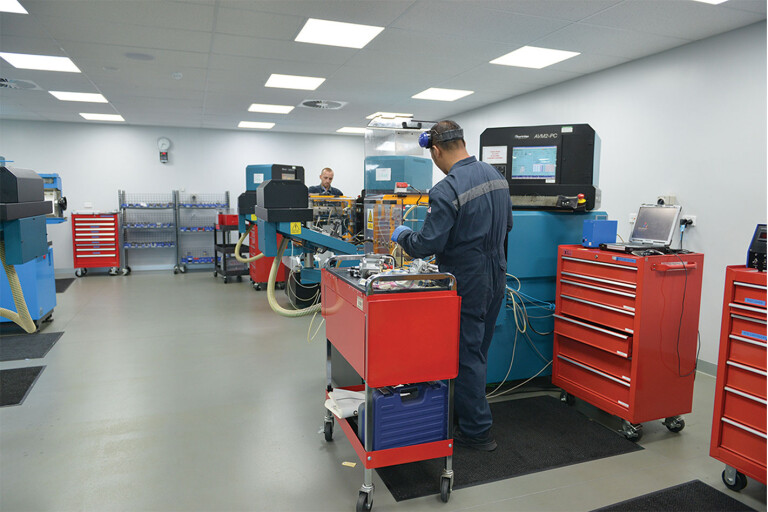
AT THE FRONT END
THE CONFIDENCE in its product is another mainstay of the brand, with its exchange units built to OEM standard thanks, again, to its comprehensively equipped premises. This includes authorised tooling and equipment to test and repair the latest tech from big-name companies such as Bosch, Delphi, Denso, Stanadyne, Yanmar, VDO and Zexel. The vehicle workshop is packed with a full range of diagnostic scan tools to cover most Japanese and European applications. The workshop includes two quick diagnostic bays, 10 vehicle bays, three truck bays, the aforementioned 4WD dyno and a Bogie Drive dyno.
In terms of a one-stop shop for all your diesel requirements – and performance enhancement aspirations – dropping in to check out the massive CDS HQ is a no-brainer for making those 4x4 modification and tuning dreams come true.
See www.cornells.com.au for more information.
COMMENTS