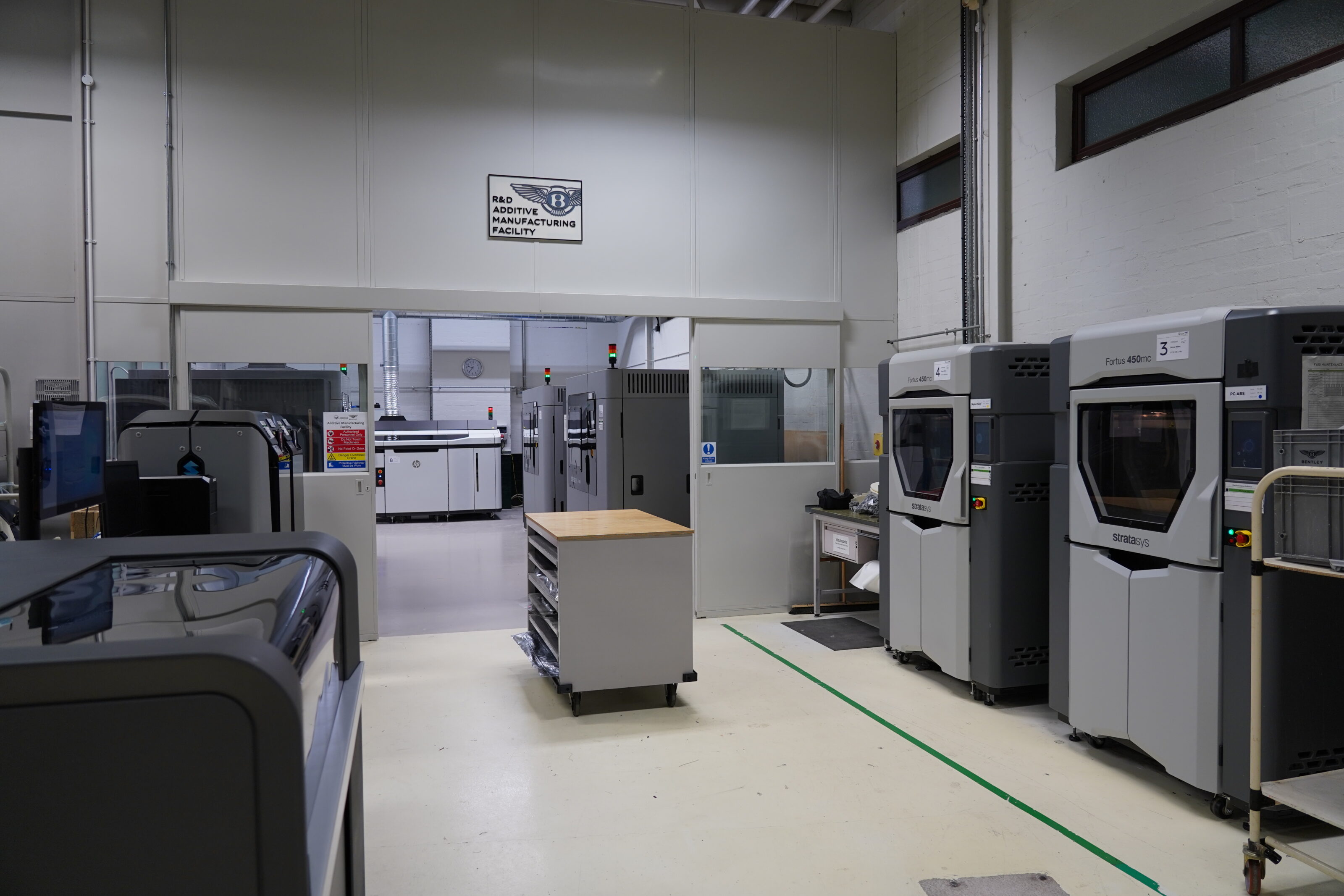
Bentley has announced it will double the production of 3D-printed components, following a further £3 million (AU$5.7m) investment into its Additive Manufacturing (AM) plant.
The facility – situated within the company’s headquarters in Crewe, England, where all Bentley models are produced – was opened in 2013, with production now expanding beyond the first two 3D printers.
More than 15,000 components were manufactured at the plant in 2021 alone, with the investment allowing Bentley customers to bring even greater personalisation to their cars.
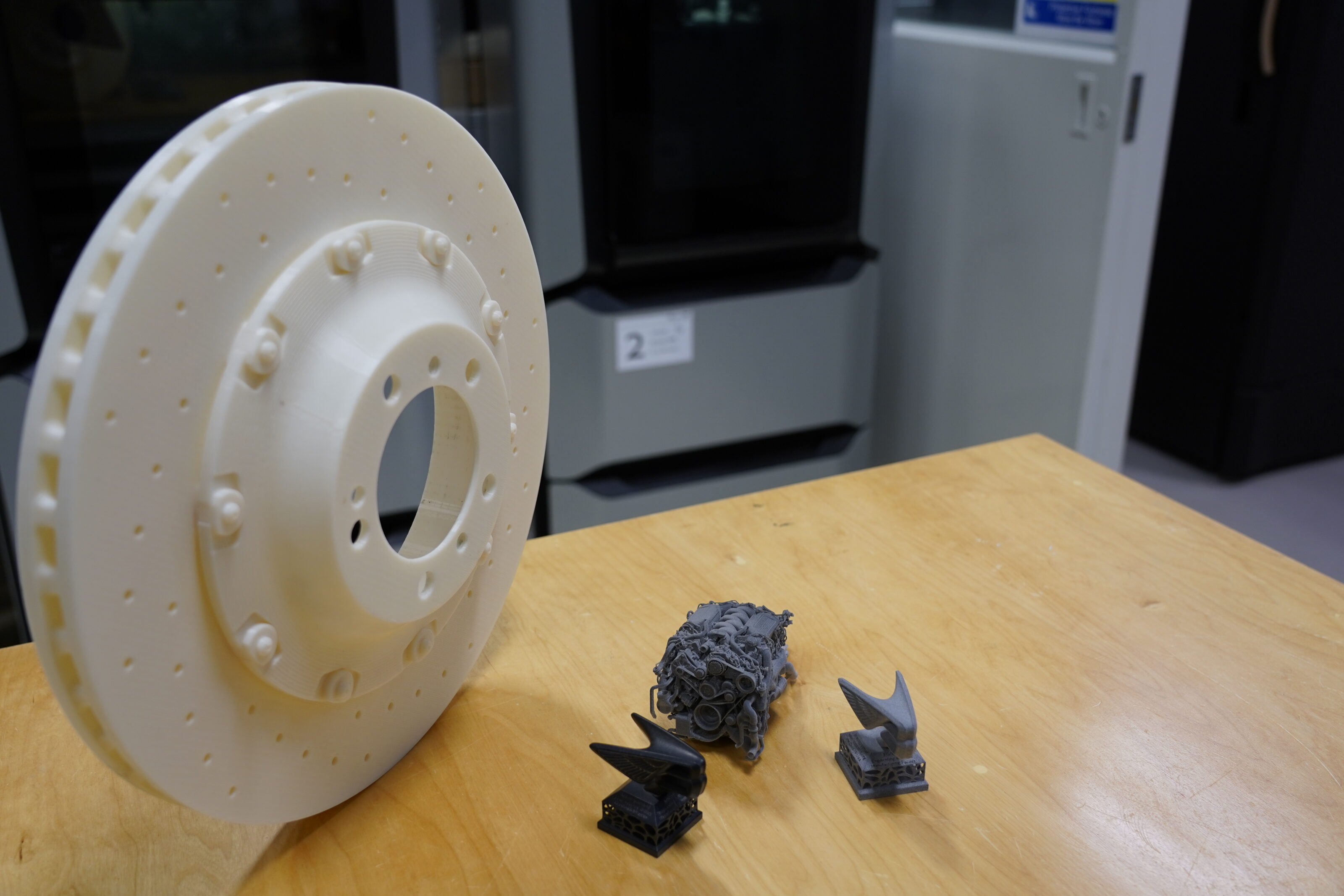
In addition, Bentley says its workers are now offered Additive Manufacturing training to understand how it could benefit the processes used in their work.
The process works through converting 3D CAD models developed by Bentley into physical components, with existing designs used across a broad number of categories, including; lightweight sanding blocks for Bentley’s wood shop, historically-accurate parts for the Bentley Blower Continuation model, and face shields provided to the healthcare sector due to the COVID-19 pandemic.
Other parts produced using 3D printing technology include physical components for powertrain and vehicle prototypes, and parts for the record-breaking Bentley models driven in the difficult Pikes Peak Challenge in the United States.
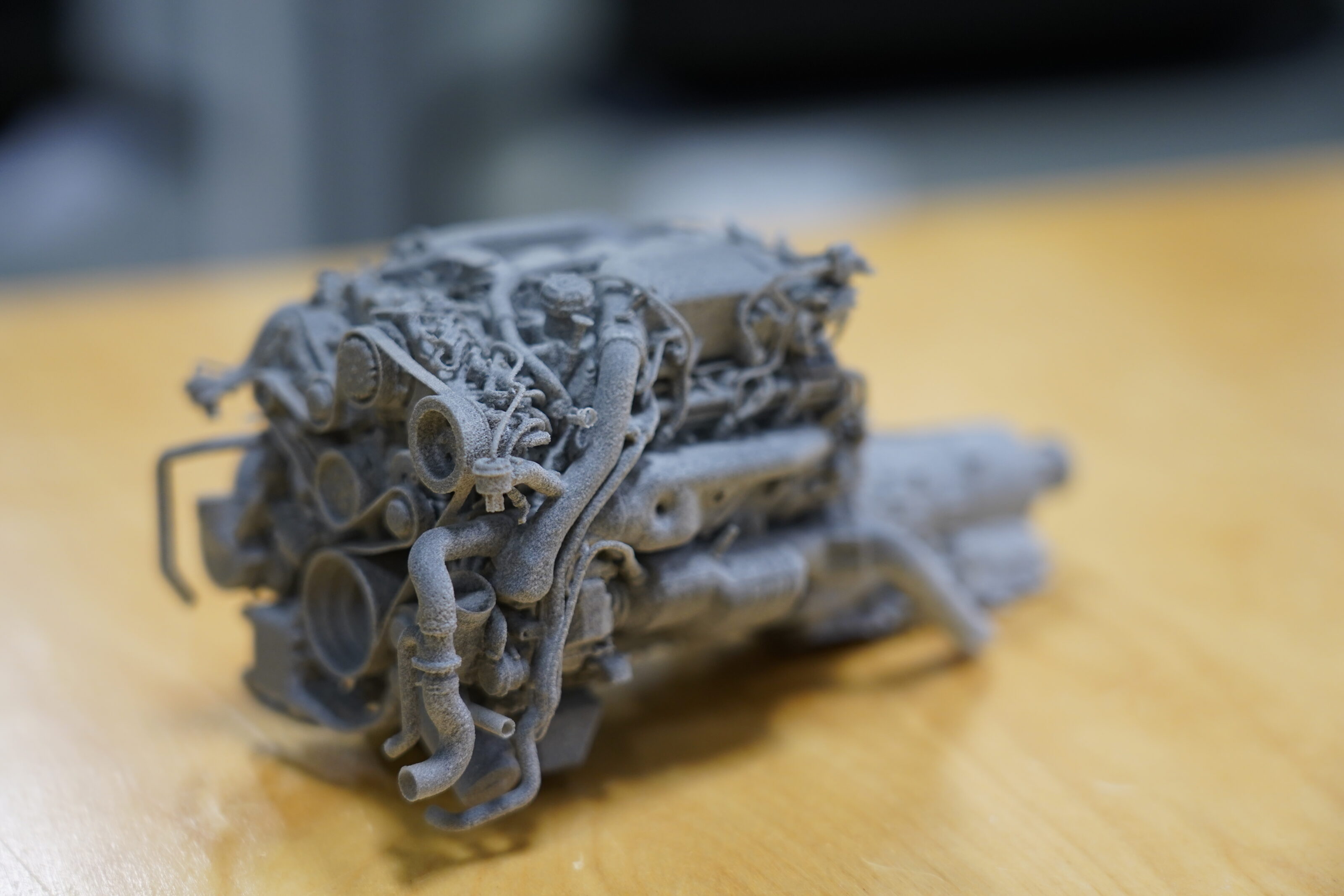
“This latest investment is also making a significant impact with our colleagues from across the company, helping to create advanced assisted tools to drive continuous improvement throughout manufacturing processes,” said Peter Bosch, member of the board for manufacturing at Bentley.
“As we look to the future, there really is huge potential to where this advanced technology can progress, including having a greater ability to personalise parts for our customers and further enhancing the individualisation programme offered on every car.”
The marque claims 3D printing halves the cost of parts and operates around the clock, allowing it to produce thousands of components using more than 25 different materials.
We recommend
-
Car Style
3D printing and the automotive industry
No longer just a means of making one-off prototypes or wild concepts, 3D printing is now a part of the automotive production line
-
News
Ford releases 3D printing files for Maverick accessories
Blue Oval puts interior functions into owners hands
-
News
Ford Australia backs health workers in COVID-19 battle
Production of face shields kicks off at Broadmeadows with 100,000 units pledged for health workers