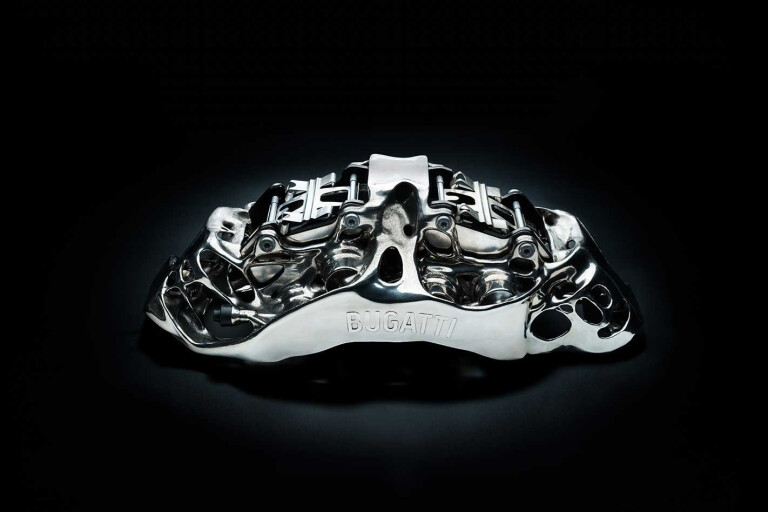
French hypercar builder Bugatti has created a titanium brake caliper using a 3D printer.
It claims to be the first manufacturer to have created one using printing technology.
The caliper is a functional size, measuring at 41cm long, 21cm wide and 13.6 high, but it only weighs 2.9kg.
The aluminium caliper Bugatti is currently using weighs 4.9kg, and its material isn’t as strong.
And since Bugatti isn’t known for rushing its build process, the 56 hours (45 to print, and 11 to machine the surfaces) it takes to create a caliper shouldn’t bother the line workers.
The width of the material walls on the component range between one and four millimetres.
Head of new technologies in the Bugatti Technical Development Department Frank Götzke says being at the forefront of technology is important to Bugatti, and this brake caliper is just the most recent example of that.
“It was a very moving moment for the team when we held our first titanium brake caliper from the 3D printer in our hands,” Götzke says.
“In terms of volume, this is the largest functional component produced from titanium by additive manufacturing methods.
“Everyone who looks at the part is surprised at how light it is – despite its large size. Technically, this is an extremely impressive brake caliper, and it also looks great.
“In 3D printing development, Bugatti is the leader in the Volkswagen group.
“Everyone can and should benefit from our projects. This is also part of Bugatti’s role as the Group laboratory for high-tech applications.”
“We have not only developed the world’s largest titanium component produced by additive manufacturing but also the longest aluminium component to date made by 3-D printing.”
In addition to the caliper, Götzke says Bugatti has also created a ‘lightweight aluminium windscreen wiper board’ using the printing process, and it weighs 400g, half the weight of a conventional wiper board.
COMMENTS