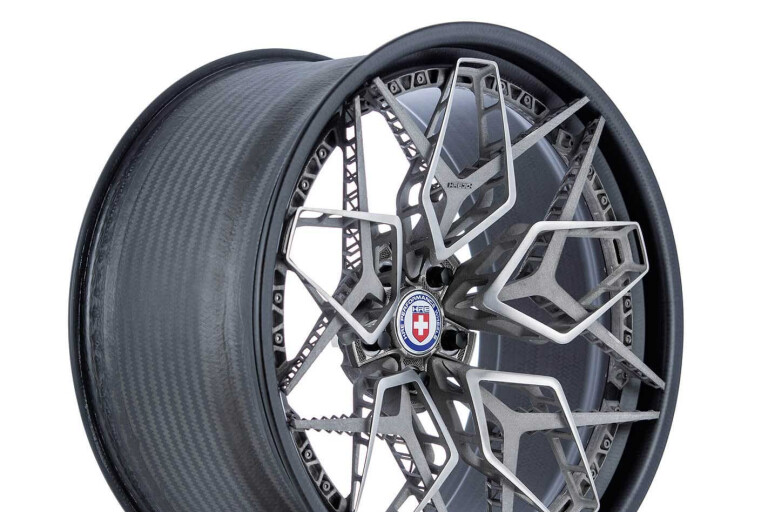
US-based HRE Wheels has teamed up with AddWorks, a department of GE’s material additive company, to create the world’s first 3D-printed aluminium wheel.
The companies hope this specific process, known as Electron Beam Melting (EBM), will change the way wheels are manufactured.
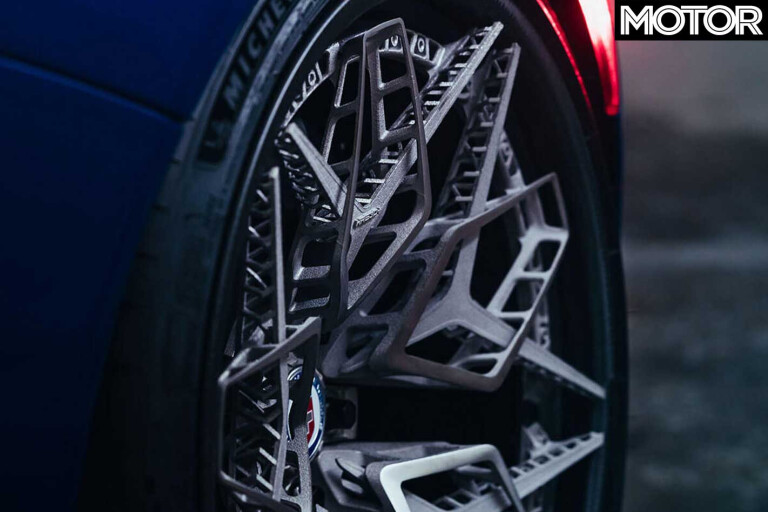
HRE says a traditional aluminium ‘HRE Monoblok’ wheel, around 80 per cent of a 100-pound forged block is removed leaving a 20-pound wheel, around 9kg to us. But with additive manufacturing, or 3D printing, only 5 per cent is removed and can be recycled.
Titanium has a higher specific strength, HRE adds, meaning the wheel can use less material and be lighter.
HRE President Alan Peltier also says it allows the designers more freedom with the design of the wheel itself, now that the process of manufacturing is changed.

"This is an incredibly exciting and important project for us as we get a glimpse into what the future of wheel design holds,” says Peltier.
“Working with GE Additive’s AddWorks team gave us access to the latest additive technology and an amazing team of engineers, allowing us to push the boundaries of wheel design beyond anything possible with current methods.
“To HRE, this partnership with GE Additive moves us into the future.”
GE Additive AddWorks senior design engineer Robert Hanet says AddWorks worked with HRE due to the wheel manufacturer’s stringent quality standards.
“HRE prides itself on its commitment to excellence and superior quality in the marketplace.
“It was a natural fit for AddWorks to work on this project with them and really revolutionize the way wheels can be designed and manufactured.”
COMMENTS