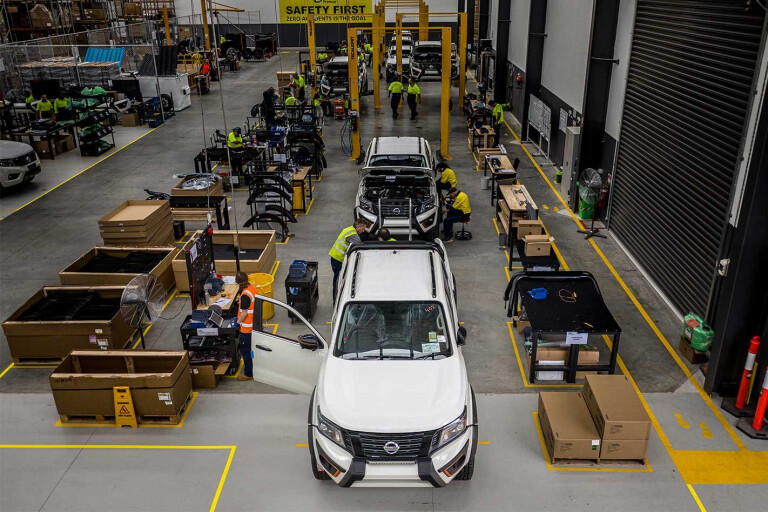
“Sometimes you have to put your balls on the line,” reveals Bernie Quinn, the head of automotive engineering and assembly company Premcar. The casual, almost matter-of-fact comment refers to the multi-million dollar investment in facilities, staff and equipment in the still-fresh factory I’m entrenched in, ready to get my hands dirty.
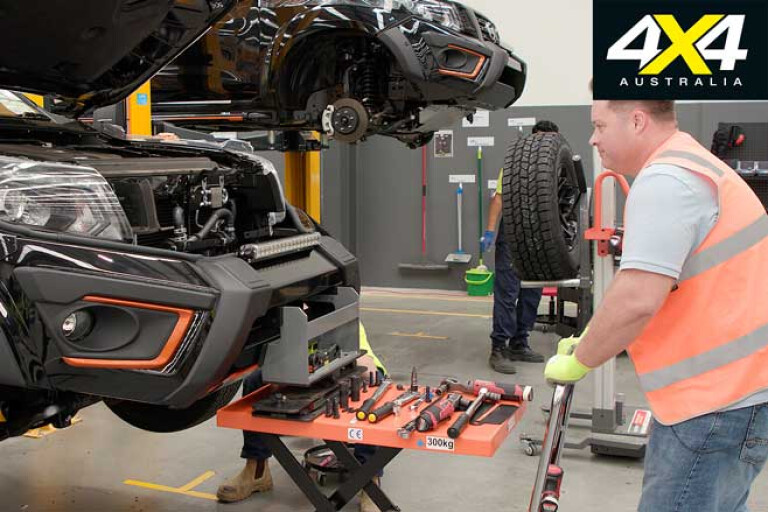
Every few minutes Nissan’s latest tough truck, the Navara N-TREK Warrior, flickers past in the background, moving around the sizeable 6300-square-metre facility in the north of Melbourne. We’re in the boardroom with its large screen TVs and slick furniture that is a far cry from the bustle of the assembly line only metres away. Both are a world away from the grunge and disorder some might envisage of an automotive workshop.
Created from the ashes of the Tickford business that once crafted hot Falcons, Premcar has turned its attention to the booming off-road segment currently dominated by dual-cab utes.
The first major client is Nissan, keen to exploit the potential of the Navara. Rather than throw accessories at it to beef up the look, Premcar sliced and diced with suspension and chassis modifications and enhanced underbody protection as part of comprehensive engineering program aimed at boosting off-road performance.
In one unused corner of the workshop are some dormant vehicle hoists, each brand new. It’s a rare sliver of space where there’s not much happening. Pointing to some telltale tape on the ground, production manager Bill Birney says that’s where a wall will soon be built for the planned engineering facility, all of which helps paint the bigger picture of what Premcar is about.
That planned engineering space is the brains behind the brawn that is the manufacturing facility. It is key to Premcar’s investment.
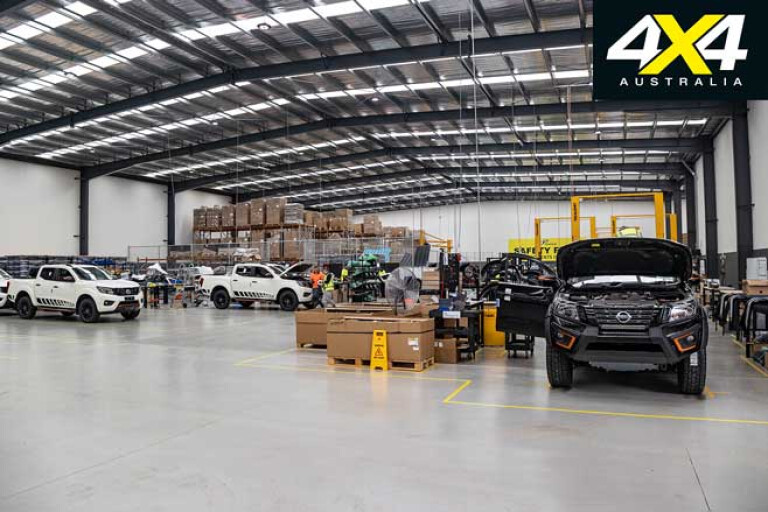
Rather than an aftermarket attack using quality componentry, the N-TREK Warrior work adheres to Nissan’s global factory standards, requiring additional checks and quality measures to keep the Japanese masters content.
Hence the investment, one Quinn says was sharpened for the Warrior deal to learn the ropes of what he clearly hopes is a bigger world of manufacturer-approved modifications.
“We sacrificed some margin on this program and made some long term commitments on facilities and investment that’s going to force us to work harder to keep us busy,” he says, adding that taking a punt is part of his approach to business.
“I’ve never regretted taking a risk, I have regretted not taking a risk.”
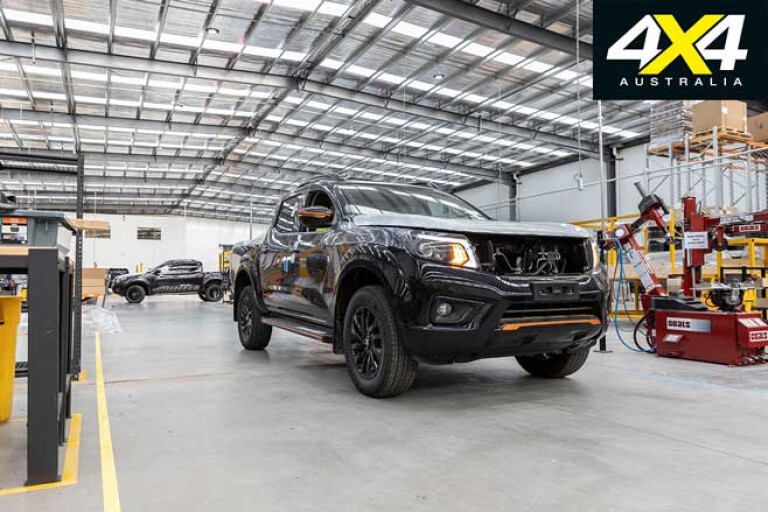
The Warrior deal runs until the end of the year, prompting Quinn’s leap into a brave new world. However, with an updated Navara expected by 2021, provided things are selling strongly there’s a good chance there will be a Warrior 2.0 – from the same (expanding) facilities.
This is as close as we get to vehicle manufacturing in 2020 Australia. In the wake of a horror decade for manufacturing in Australia the Premcar business is a rare bright light. Granted, it’s a minnow compared with the sprawling Toyota, Holden and Ford factories that were once churning out hundreds of cars a day. Instead, Premcar’s target is 13 vehicles, or one every 34 minutes from its full-time staff of 40 personnel. That’s glacial by global standards, but looking at the truncated 11-station assembly line there’s no shortage of activity.
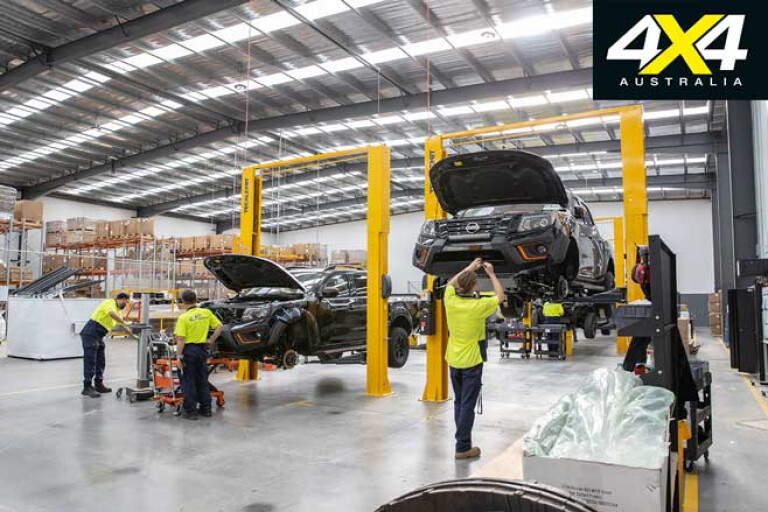
It’s as I’m wielding a strut assembly for the front suspension system that this 34-minute target becomes more pertinent. Unbolting the lower suspension system to allow removal of the factory-fitted unit and replacing it with the new one takes a matter of minutes. Then there’s bolting on the larger bump stops and tweaking other components as part of the rigid process.
It’s then retightening everything using pre-programmed torque wrenches. A chalk pen marks the bolts as correctly fitted, the final piece of a manufacturing process that is meticulous at every step. Those chalk marks are crucial.
Clearly a stickler for rules – the “Safety first” banner taking up half the wall at the end of the workshop is testament to that - Birney reveals he’s stopped cars at the end of the line for not having the appropriate chalk marks. The work may have been done, the components fitted and the bolts tightened – but without that visual confirmation that things have been completed to the book, the car is unfinished and sent back for a recheck.
“We inspect to a very high level,” says Birney, formerly from Ford and someone who has worked at a Chinese automotive factory and seen things done on a massive scale.
Like any first-class manufacturing facility Premcar monitors things down to the minute. It’s that big factory thinking that has led to the Warrior production line, itself an evolving facility.
“We’re doing the same processes that you do in a large plant … OEM-style processes.
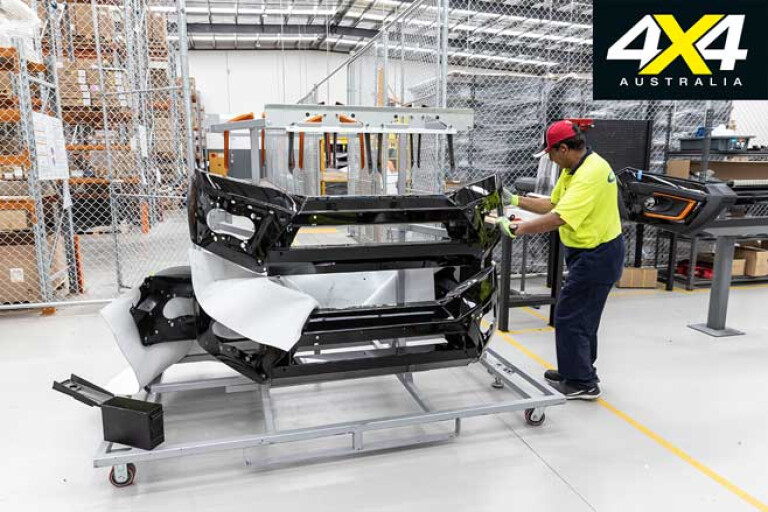
Not content with standing back and admiring the early efforts to assemble modified vehicles to a scale smaller workshops would typically not attack, Premcar turned to data and software to streamline the processes.
Days before I jumped on the spanners, the production line was reworked to unlock a bottleneck with attachment of the front bumpers. Hoists were repositioned and electricians called in to add powerpoints – all in the quest for a better flow. Other tweaks and process refinements helped shave 40 per cent off the build time, in turn increasing total vehicle outputs and lowering costs.
Yet there’s no sense of panic or rushing. Workers are fastidious in ensuring every component is seated correctly and performing its intended function.
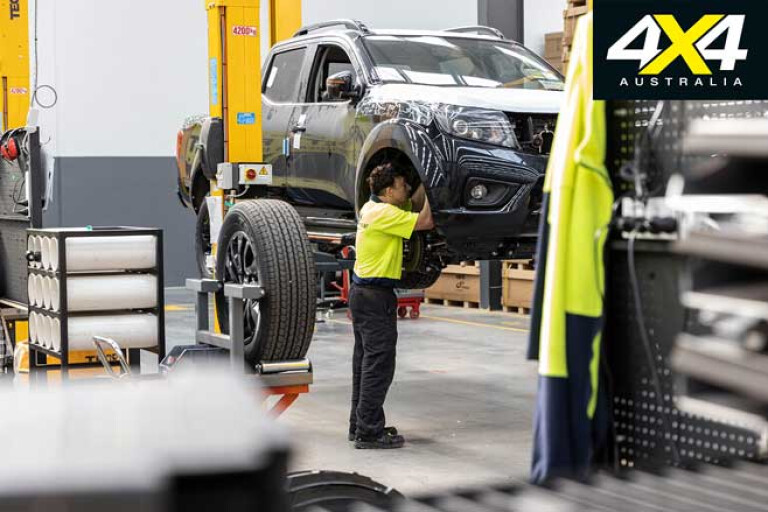
One thing missing from a typical car factory is sparks and noise. There’s not a robot in sight, with humans the ones brandishing rattle guns and wrenches. And things are borderline quiet, save for the occasional staccato woosh of a tyre being inflated or double beep of a horn before a car starts moving. Along with hazards flashing the latter is a simple way to warn of incoming traffic.
It’s clear the all-important processes and people behind the Premcar Warrior have modelled everything off a full-scale factory. Trucks arrive daily to deliver components for the upcoming builds and there are stacked shelves with spares in case something goes MIA.
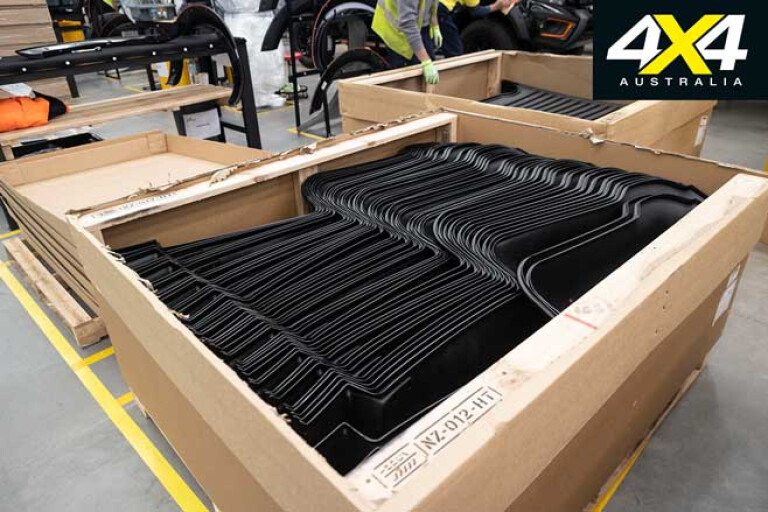
Removed components – such as suspension struts and front bumpers – head back to Nissan to be recycled or sold as second-hand parts.A skip bin sidles past me loaded with recycling. Premcar even found a local business recycling foam packaging, ensuring something more useful than taking up space in landfill.
Trolleys and wheeled stools are all about reducing worker stresses and strains and there’s a cleanliness and order to every inch of the facility. Not that anything is manufactured here. Every component is sourced externally. It’s only the occasional reworking – such as some trimming of the inner ‘guards of the wheel arch – that occurs onsite.
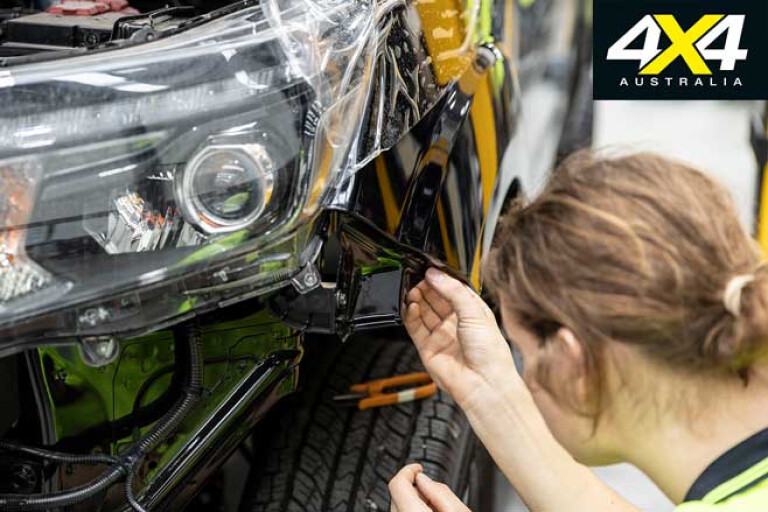
Additional components are either sourced from Nissan’s parts catalogue and modified – such as the front bumper – or sourced from top tier suppliers. The bumpers are painted by the company that once painted components for HSVs, for example. And the tow bar assembly – redesigned to accommodate the larger spare tyre that matches those on the car – is from respected canopy and bar supplier EGR.
Watching the prep work on the front bumper assembly reinforces the quality of the suppliers. The bar starts as a Nissan factory component but one that is modified to do without the upper hoop, instead fitting plastic stubs for aesthetics. By the time a Hella LED light bar is added it’s a 65kg component ready to be bolted on. Everything blends beautifully and the finish of the plastic and matching of colours is in line with components fitted to the Navara at the Thai factory.
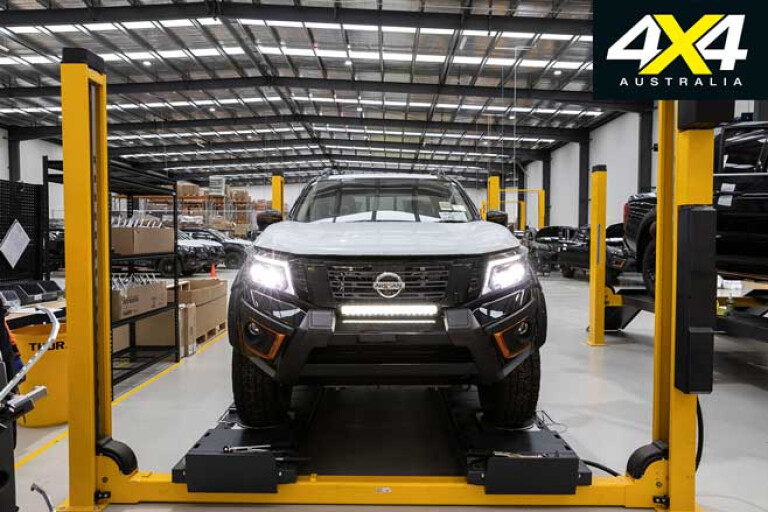
One of the final stations adds some electrical hardware to recalibrate the speedo, which would otherwise be out of whack due to the larger rolling radius Cooper Tires rubber.
Just as I’m getting into the bolting and swivelling groove I get shown the hand towards the end of the production line. It’s the station were the ‘stripers’ do their work; those people who used to fit stripes to FPVs but now add the stickers and decals to a Warrior. While it may seem simple, there’s an art to ensuring such a large sticker lands in the precise spot without dirt or grime between it and the paint. Only three people in the Premcar facility are trusted with the sticker placement – and two of them are women.
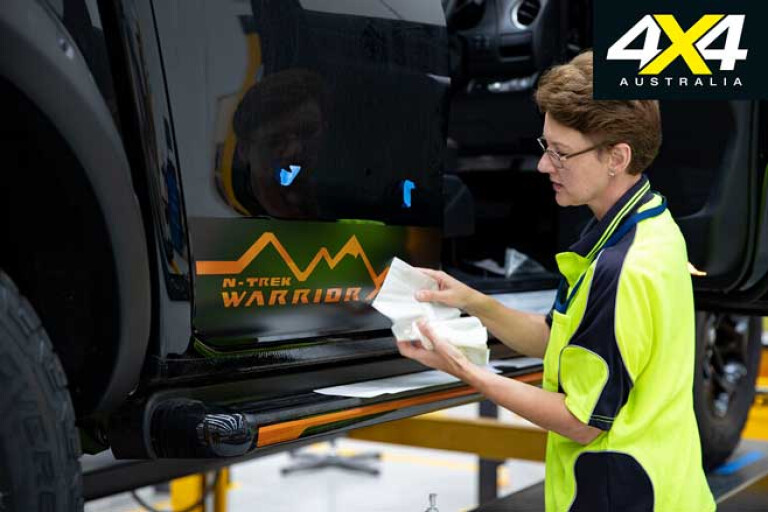
“You need a really steady hand … you need good attention to detail,” says Birney.
From there every car undergoes a short test drive and quality check to ensure all components and additions are done to those processes and are doing what they say on the box.
All before a customer – or one of us - gives it a proper test drive. One involving red dirt and Aussie corrugations. The sorts of things guaranteed to test the mettle of any 4x4.
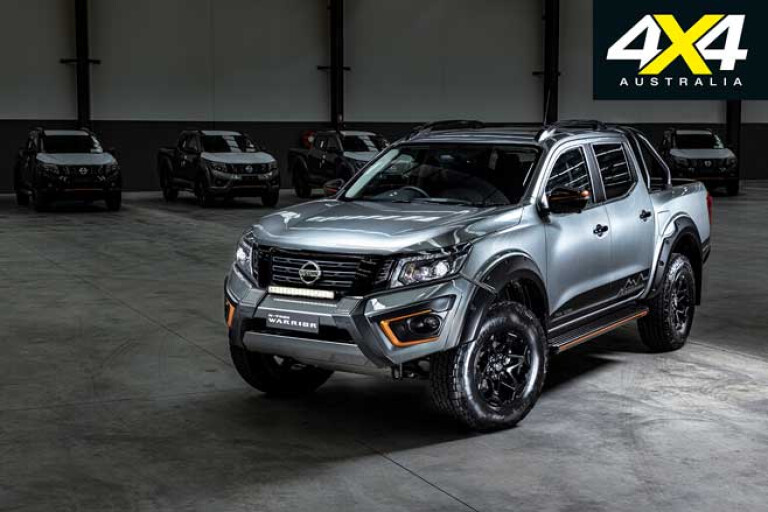
COMMENTS