The Tohoku earthquake that struck Japan’s east coast in 2011 was the most powerful earthquake ever recorded in Japan. A tsunami devastated the mainland, inundating the Fukushima nuclear reactor and causing huge loss of life.
Amid those headlines, it was perhaps inevitable that the resultant closure of a nondescript factory manufacturing bismaleimide triazine (BT) would be overlooked.
Mitsubishi Gas Chemical manufactures more than half the world’s supply of BT, a resin required for making substrates that connect chips to printed circuit boards. Automotive companies suffered months of delays trying to rebuild the crippled supply chain.
More coronavirus news
- How to minimise COVID-19 exposure in your car
- Industry reels from coronavirus as Elon Musk scoffs
- Australian Grand Prix cancelled after COVID-19 case confirmation
Tesla has been forced to supply some Chinese-built Model 3s with Hardware 2.5 rather than Hardware 3.0, leaving a system 21 times slower without the entire suite of Full Self-Driving capabilities.
Tesla’s Shanghai Gigafactory resumed production on February 10. And customers who received the downgraded hardware were asked to make an appointment at a Tesla Service Centre and wait patiently for a retrofit.
Mercedes-Benz sounded a note of caution in its assessment of coronavirus risks. “Risks for the Daimler Group may not only affect the development of unit sales, but may also lead to significant adverse effects on production, the procurement market and the supply chain,” the Stuttgart-based company said in its annual report.
The largest human containment exercise in history was inevitably going to have effects on the automotive supply chain. Not so well understood is that the non-linear nature of supply chains means a month-long shutdown does not mean a month’s delay in products reaching consumers.
Even the failure of a tier four supplier can shut a production line. However, lessons learned from the Tohoku earthquake resulted in a number of damage-reducing measures to cut disruption risks.
The first was a focus on smarter risk management. Closer partnerships with suppliers, multiple suppliers for the same component and a risk-balanced supply chain with standardisation of processes and operating practices became the norm.
Secondly, there was a realisation that the convergence between automotive and tech industries meant the two branches were often competing for supplier capacity. And tech was often the stronger partner.
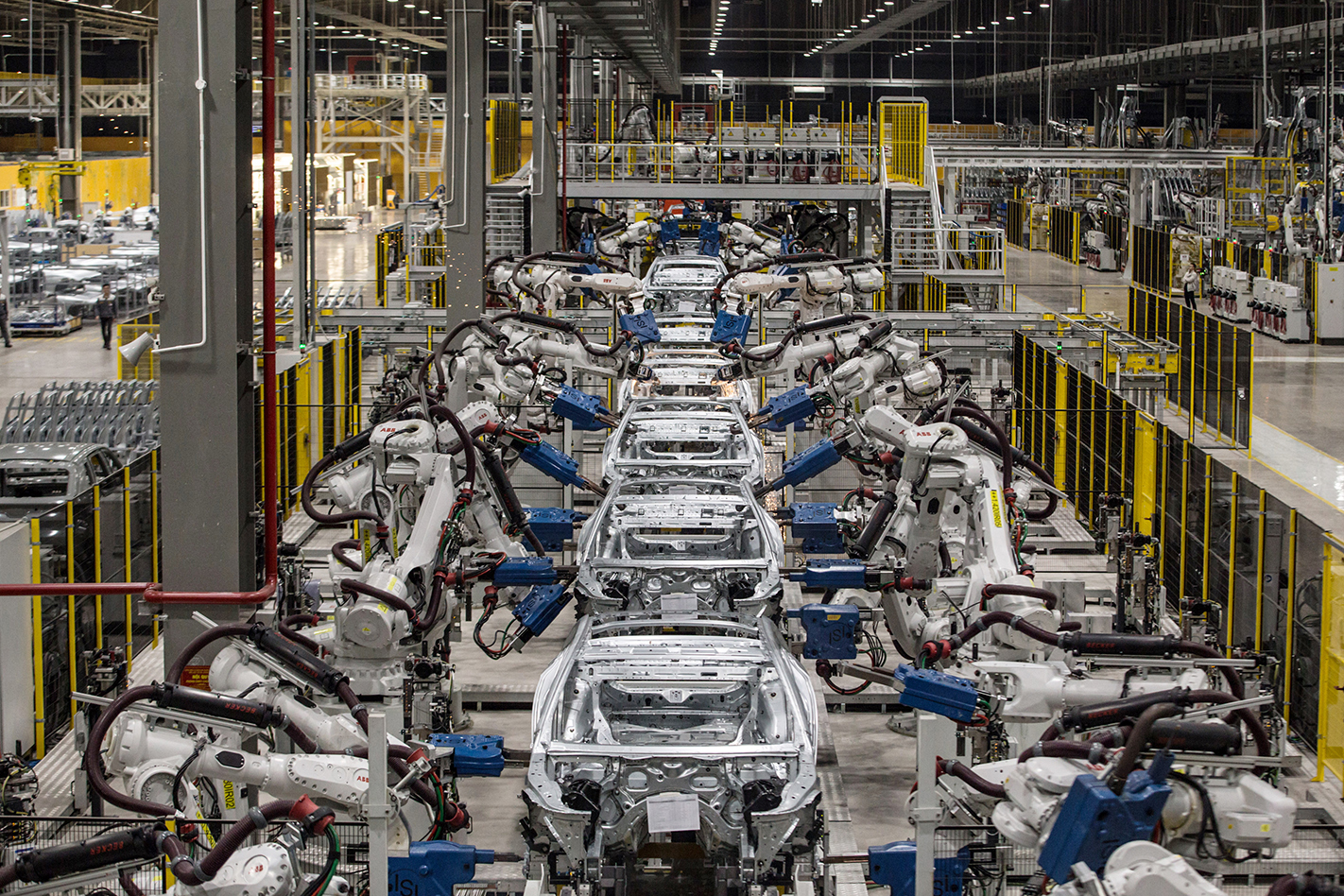
Unfortunately, an integral part of the Japanese car industry’s risk mitigation strategy was to increasingly rely on South Korean and Chinese suppliers.
This is set to result in at least six months of acute supply chain disruption. One unexpected balancing factor was a local collapse in demand. Car sales in China plummeted 80 percent in February as the coronavirus epidemic stopped footfall through dealerships.
Here in Australia, rating agency Moody’s has predicted that new car sales will be down 2.5 percent this year, on the back of a 4.6 percent drop last year. A previous estimate that the sales decline would slow to 0.9 percent was changed due in part to supply chain effects of COVID-19.
Coronavirus is far from the only glitch in the supply network. Mercedes-Benz had to put the brakes on $50 million worth of vehicles late last year after they were found to be harbouring exotic heath snails, while detections of brown marmorated stink bugs in vehicle shipments from south-east Asia remain on the rise.
The switch from the New European Driving Cycle (NEDC) to Worldwide Harmonized Light Vehicle Test Procedure (WLTP) has also had a supply-side knock-on effect since 2018, with many vehicles withdrawn from sale in Australia.
Ironically, it appears to be the Volkswagen Group that is hardest hit by the switch to WLTP, with many Skoda, VW and Audi models being deleted due to a business focus on getting higher-volume models WLTP tested first.
One of the less obvious coronavirus effects is the supply issue around automotive parts for the repair and maintenance industry. It is about to become significantly more expensive, and considerably more difficult, to repair vehicles with new parts.
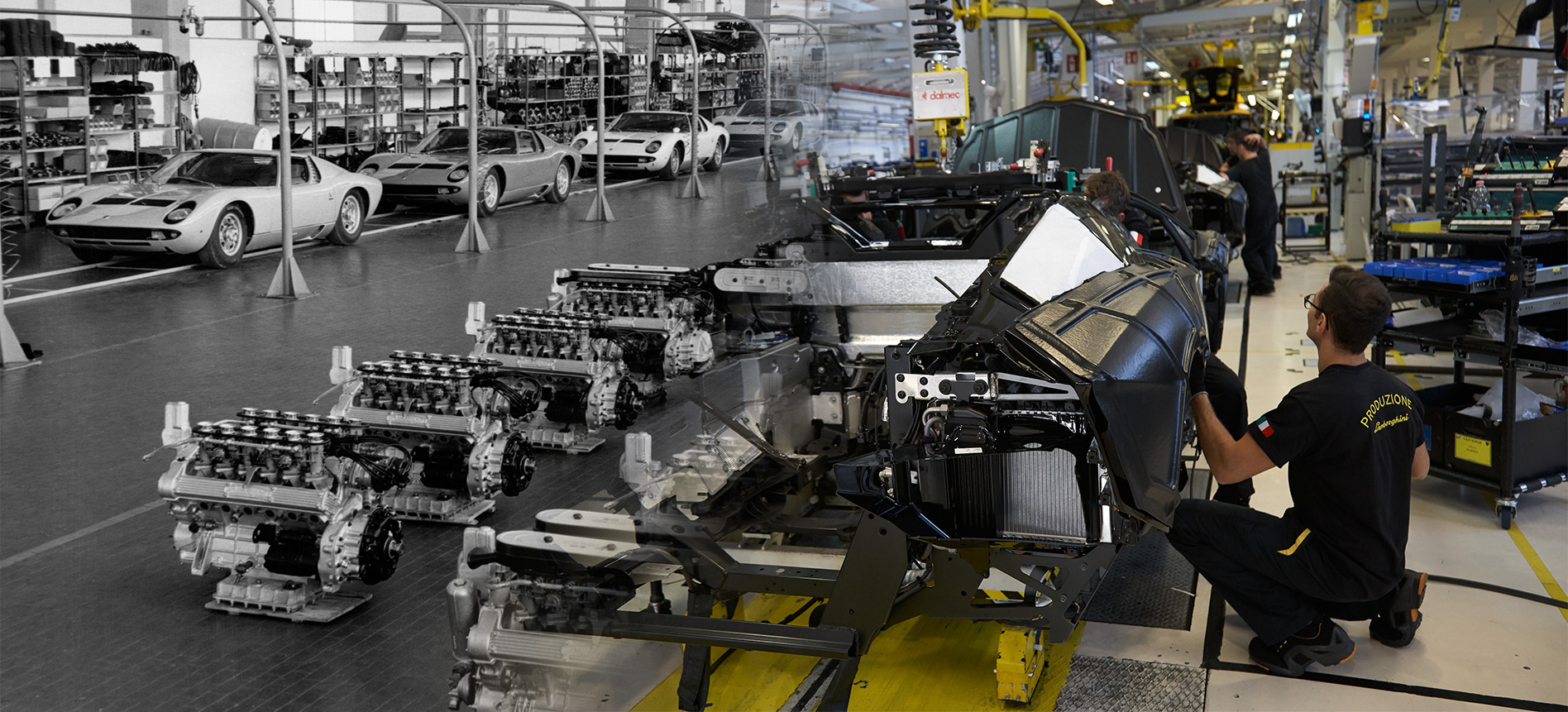
A solution to this looming crisis is to increase the availability and use of recycled original equipment (ROE) parts.
The challenge is in converting the Australian public, insurers, mechanics and suppliers of ROE parts to the potential impacts of this surge in demand, such as avoiding the unwitting sale and installation of spare parts that have been recalled due to faulty manufacture.
“You cannot complete a repair unless you have every part required for that repair, so just one part not being available out of hundreds that can be used in a repair, will affect the total claims cycle,” says Chris Daglis, managing director of All Auto Recalls.
Fortunately, every supply chain challenge serves to reinforce backups for the next bump in the road.