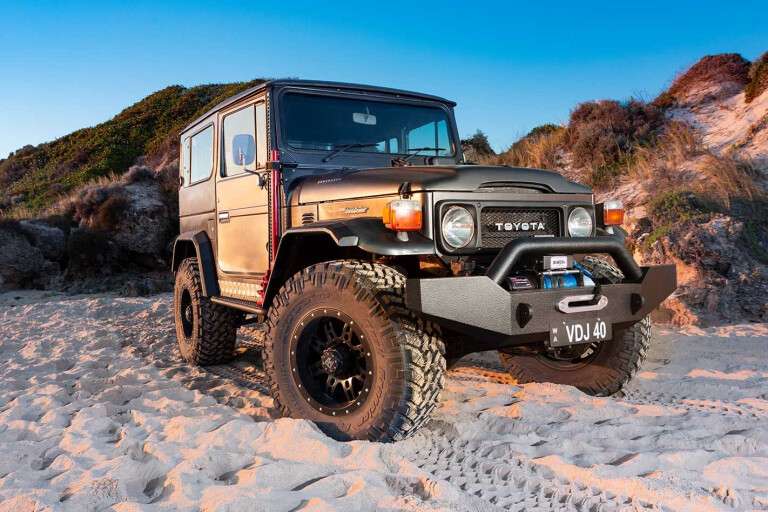
Being told “it can’t be done” is like the proverbial red rag to a bull, but for Perth-based brothers Harpaal (Harry) and Sarpal Gill, that saying just doesn’t fly, as this incredibly cool 1979 BJ40 Cruiser proves.
In truth, this vehicle is probably a dream for most off-roaders. Take one 4x4 that is regarded worldwide as one of the true 4x4 icons and update it for off-road touring and daily driving.
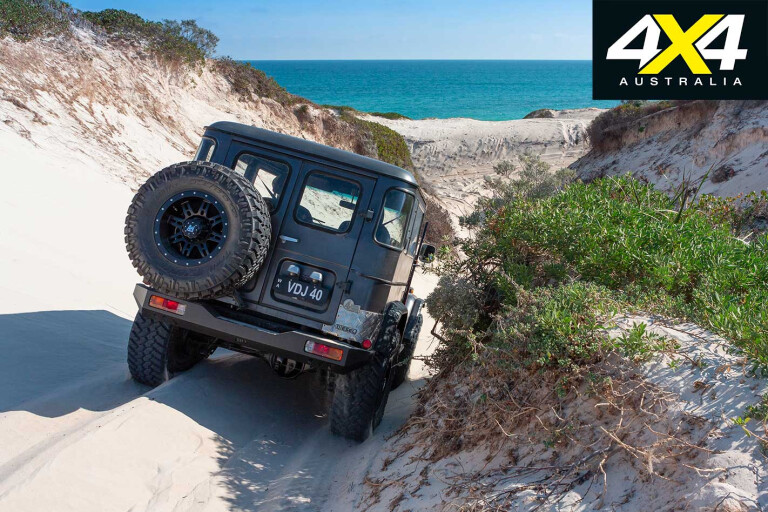
And when we say update, we mean the Full Monty: shoehorning a 4.5TDV8 from a 79 Series Cruiser into the engine bay and then building a fully custom suspension system – highlighted by the trick four-link rear with Nolathane bushing – makes this BJ a distinct one-of-a-kind off-road bruiser. And all it took was a belief that anything is possible, and then knuckling down and just building it...
PROVING A POINT
The Gill brothers aren’t new to tackling the impossible, having been involved in a number of unique vehicle builds over the years: search YouTube for the Gill brothers’ crazy Mahindra MM540 – an Indian variant of a Jeep Wrangler – with custom chassis and 14-inch hydraulic-lift suspension.
Their combined skillsets include metal fabrication, metal machinist, draftsman, mechanic and hydraulic fitter – all pretty handy when it comes to tackling a project such as the BJ40, and helped even more by owning their own automotive repair and tyre outlet, allowing them to keep it all in-house.
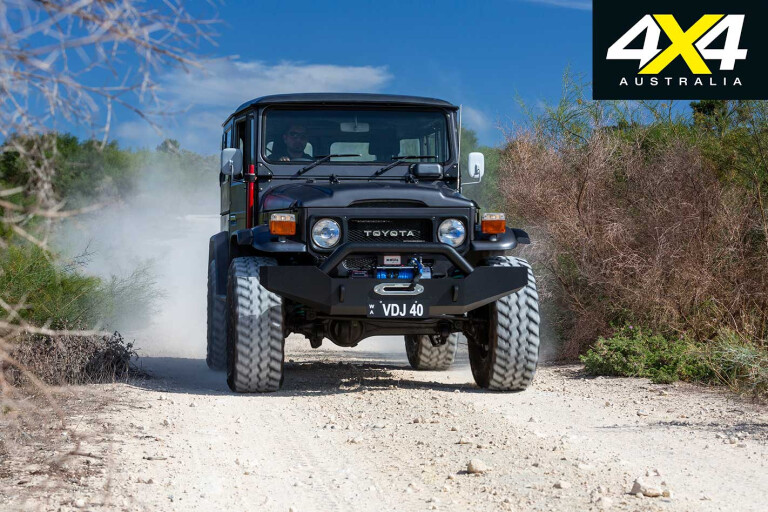
“I kind of enjoy the design,” Harry says when asked about the choice of BJ40. “I was a huge fan of the 40 Series from a long time ago. I always wanted to build up an old one but we sort of had this idea – why don’t we try this? So, yeah, it was like a childhood dream.”
The combination of a very well-proven original vehicle and an all-new (for it) but also well-proven drivetrain was the aim of the brothers’ project – and they wanted to ensure it still retained the charm of the ‘old’ BJ40, along with that ease-of-use provided by the modern LC79 donor vehicle.
Considering that first impressions of this project were daunting – Harry says most people they talked to said it couldn’t be done and not to bother trying – the actual project itself went relatively smoothly.
CHOPPIN’ AND CHANGIN’
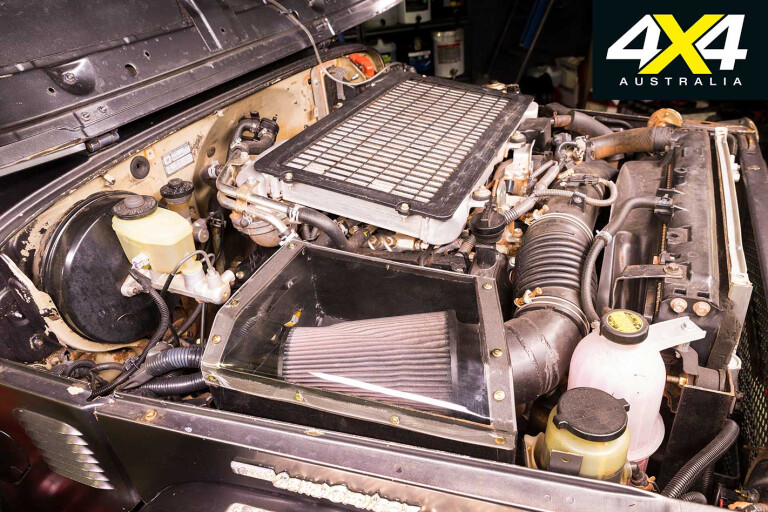
The idea of transplanting a modern 4x4’s gearbox, drivetrain and engine into what is a distinctly shorter and much older rig sounds like a whole lot of headache, starting with how to make that beefy 4.5TDV8 fit into the BJ’s engine bay without too much cutting of original BJ sheet metal.
“We started with the engine first and tried to ensure we didn’t cut anything on the body,” Harry says. “We had to place it in a couple of times in the chassis to get it where we wanted it, then started from there.”
“From there” meant also fabricating all engine mounts, the mounts (and brackets) for the five-speed manual gearbox, as well as modifying the transmission tunnel to fit said gearbox, all while making sure each and every mod would pass engineering regulations for registration.
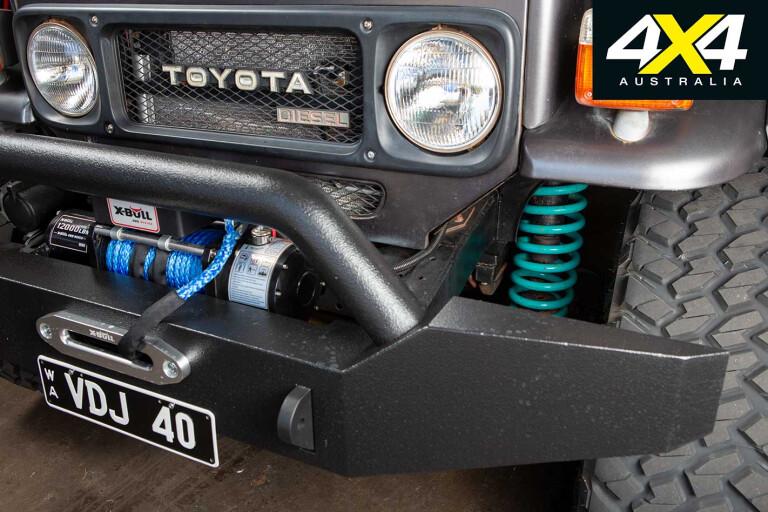
The result – after more than a few chassis cuts and mods – is an engine bay that looks factory in appearance, with only the custom air filter box and piping hinting at the transplant that has taken place.
WHAT LIES BENEATH
Deciding to build something that’s never been done before requires plenty of forethought and the ability to transfer ideas to an engineering reality. Harry called on his draftsman qualifications and AutoCAD software for this.
“We designed everything on AutoCAD,” Harry says. “So everything was designed on the computer and then we got everything laser-cut and fabricated it in the shop. It was not easy I would say, but yeah, it was fun, albeit a lot of work!”
One of the biggest parts of the project was the build and fitment of the trick four-link rear suspension setup; although, surprisingly it didn’t take as long as you’d think, thanks again to the wonders of computer design.
“For the rear setup, it took me a couple of days to draw everything,” Harry reckons. “It then took around about a week to get everything laser-cut, and then we spent another week fabricating everything. After that, it all fit perfectly.”
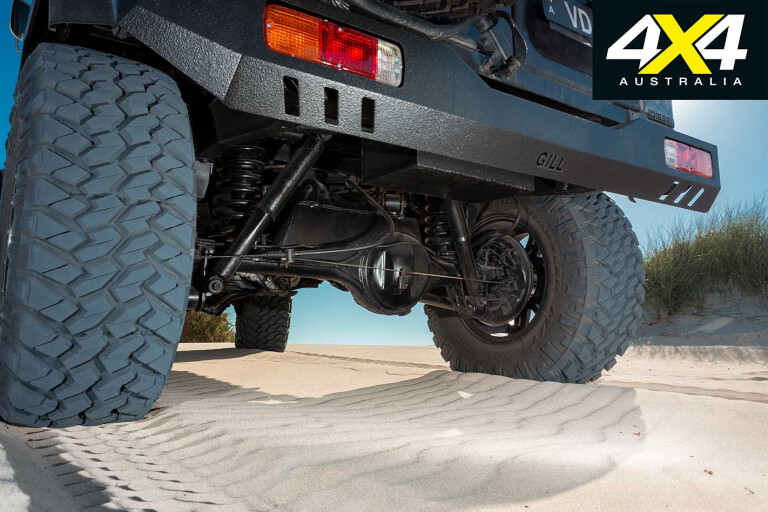
Not only does it fit perfectly, when you check out the photos of the BJ’s rear end, it looks like it came fresh from the factory – pretty impressive stuff.
The ability to work as a one-stop shop in regards to designing, cutting, building and fitting each component of this build definitely made for an easier project overall. As well as the rear suspension and engine/gearbox mounts, the brothers also designed, cut and built the front winch bar (the winch is an X-Bull 12,000lb) and rear custom bars, sidesteps and flares, with only the (again) custom-sized driveshaft and tailshaft being built by one of their suppliers (the front and rear axles are stock LC79 jobbies).
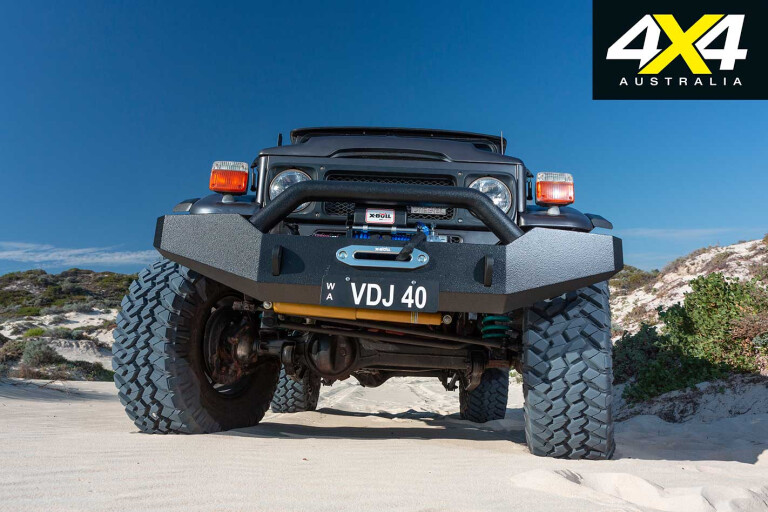
The track width of the BJ isn’t that different to the LC79, and Harry and Sarpal accounted for the difference by fitting Allied Goanna 17 x 9-inch alloys (with a 38mm spacer in the rear wheel) shod with chunky 35x12.5R17 Nitto Trail Grappler tyres. This meant the stock 79 axles (and brakes) were, in the end, a straightforward fit.
The Dobinsons dampers and springs give the BJ a 50mm lift and are a direct carry-over from the donor vehicle.
Last, but certainly not least – especially when you hear this tough BJ coming – was the full custom exhaust system. The exhaust system is a combo of factory (the headers are stock) and a three-inch custom-made mandrel-bent system, with a five-inch Hot Dog resonator, finished off with a glorious-sounding side dump pipe.
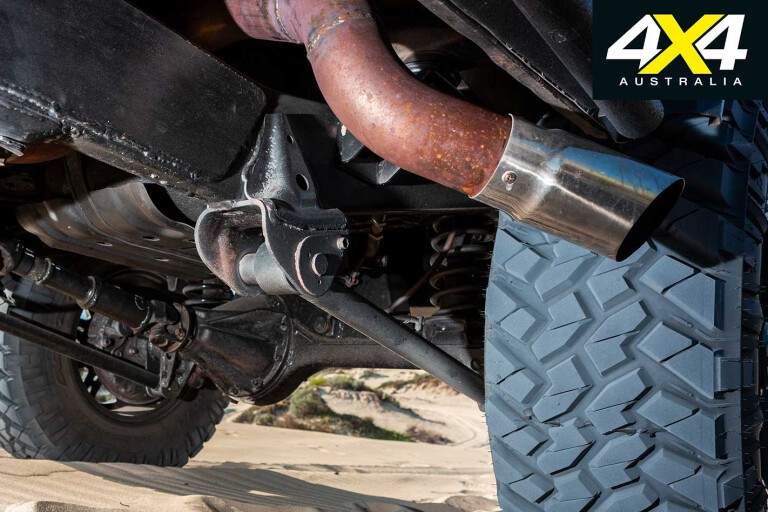
As you can imagine, space for a big-bore custom exhaust system to do justice to the TDV8 was at a premium with this shorty.
“It’s a V8, so we wanted it to sound like one,” Harry says. “We bought a few different hot dogs, a few different resonators, and a few other bits and pieces to try and see which ones sound better, which was the easy part. Then we had to modify all the bits and pieces to make it fit, but, again, it was good fun.”
IT AIN’T OVER YET
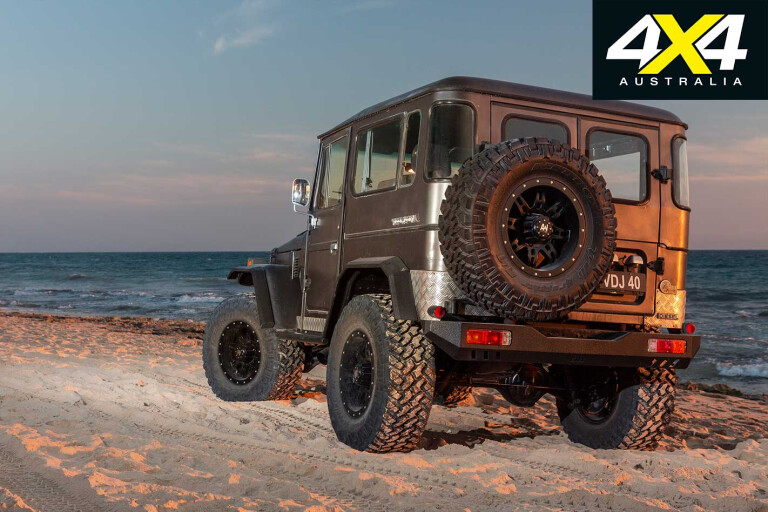
Amusingly – well, after the fact – one of the biggest hang-ups for this build was the donor LC79’s ignition key. Because the brothers didn’t have access to the donor vehicle’s original key they couldn’t reprogram the replacement to ensure it worked (the wiring in the BJ40 is a full custom job owing to the 4.5TDV8’s ECU) worked.
After getting a frightening quote from Toyota to replace the whole system (around $3K) Brendon from AutoSpark Greenwood came to the rescue, reprogramming the key in roughly 15 minutes. Other electrical work is all custom; an aftermarket central locking system ensures the BJ won’t go walkabout, while power windows offer a further touch of modernity.
The Graphite BJ40 has been on the road and tracks for three months now, but that doesn’t mean it is finished being cut, chopped, prodded and poked. Harry and Sarpal have plans to continue driving it for a few more months before it is returned to their workshop for a complete disassemble and rebuild, with the currently as-stock interior (bar the custom-made gauge fascia that fits the LC79 instrument cluster) one of the many things on the list to do, along with new suspension, another paint job and no doubt more tweaks.
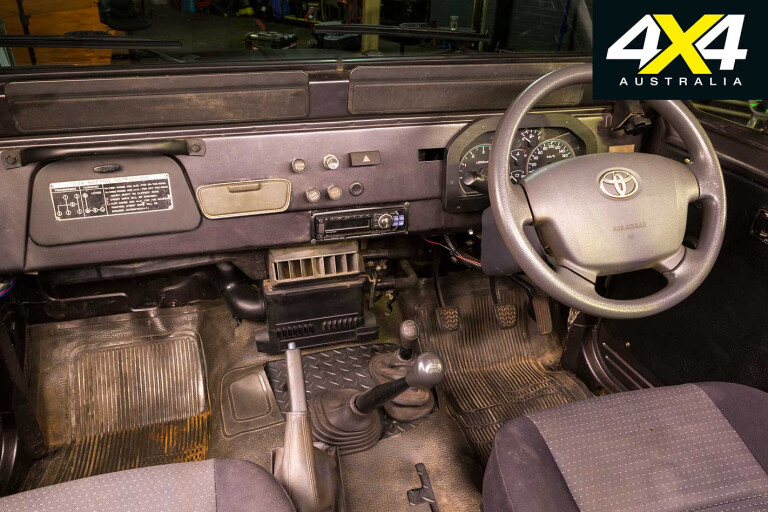
For something that was impossible, this tough BJ40 certainly looks like the perfect answer to any doubters – and if the numerous phone calls, emails and conversations Harry and Sarpal have had over the months since the big rig has been out on the tracks, it proves Harry’s point that “nothing is impossible” and that if you don’t try, you’ll never know.
When the end result is a super slick and totally unique TDV8-powered BJ40 Cruiser, you can see why it’s worth keeping those dreams alive.
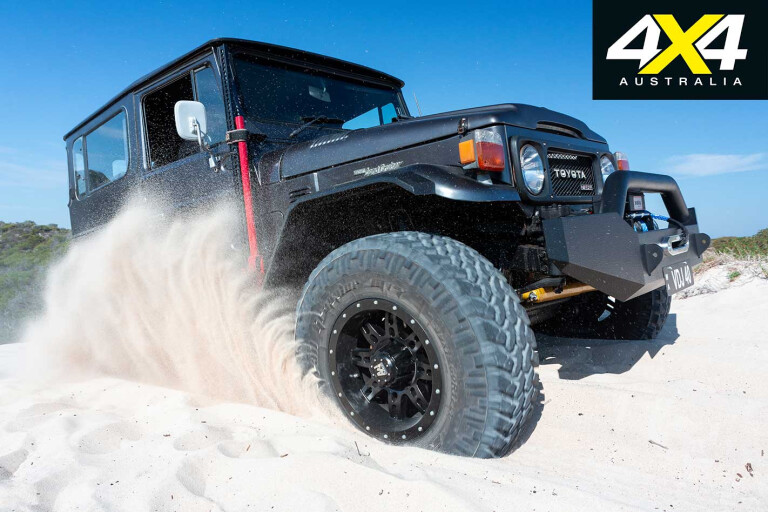
COMMENTS