
Modern independently sprung 4x4s are better in almost every way than their older live-axle ancestors.
They’re more comfortable, more capable (thanks to a whole heap of electronics), ride better, use less fuel, and allow us to pound out previously unheard-of kilometres without breaking a sweat. Yep, on paper they’re just about perfect; except all that ‘extra’ stuff comes with ‘extra’ complications.
There’s no hiding the obvious ones like needing a degree to even open the bonnet, but one that’s sprung up more and more with modern suspensions is their complication in suspension lifts.
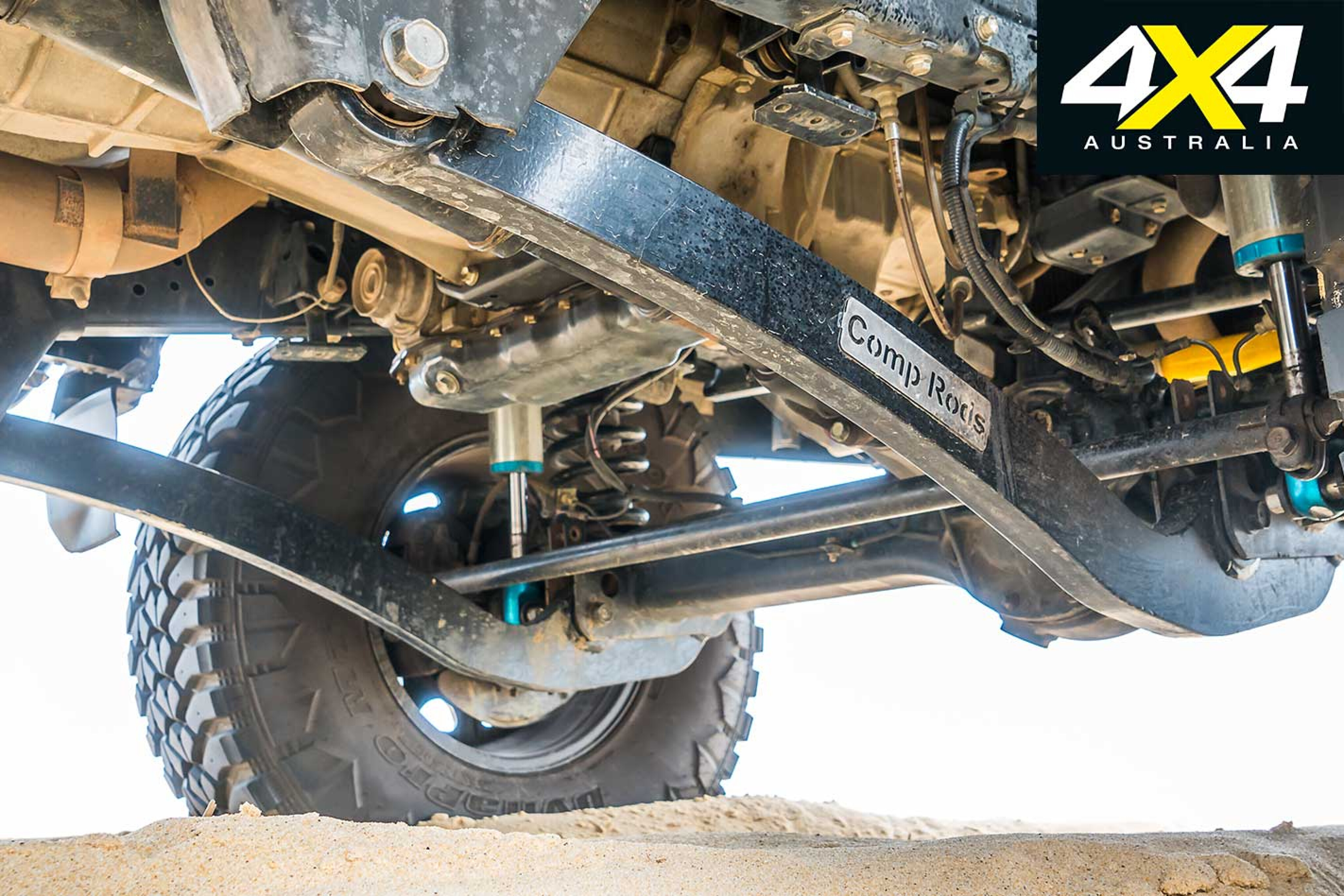
The basic premise still stands. Take out the standard springs, put some longer ones in, and lift the body and chassis of your 4x4 a few inches farther away from the ground. But unlike the comparatively agricultural live-axles, independent suspensions cause all sorts of issues when you start cranking them towards the skies.
Aftermarket upper control arms have taken the 4x4 scene by storm, promising to fix what ails you, cure your lifting issues and grow curly hairs on your chest.
To get to the bottom of what’s what, we’ve spoken to some of the biggest names in welding together control arms to find out everything you need to know to not only lift your IFS 4x4 safely, but do it legally as well.
JUMP AHEAD
- Why you do (or don't) need new upper control arms
- Legalities
- ADR compliance
- What to look for?
- Additional mods
- Improved off-road performance
Why you do (or don't) need new upper control arms
With more and more 4x4 gear being rolled in glitter and sparkles, it’s almost too easy to get wrapped up in the what and less in the why.
Before laying down your credit card details on a set of new upper control arms, it’s vital to know why you do (or don’t) need them. Whether your 4x4 is sporting an independent front end or live axle, installing a suspension lift will do two things: it’ll physically lift your chassis and body away from the mounting point of your wheels and tyres, which frees up room for larger tyres and provides ground clearance; and it’ll pivot the suspension arms, linking the two together.
In solid axles, that pivot effect is rarely an issue; the axle will roll, changing the relationship between upper and lower bearings and throwing off the caster. A set of off-set bushes will fix the issue without too much fuss. In an independent front suspension things are a little more complicated.
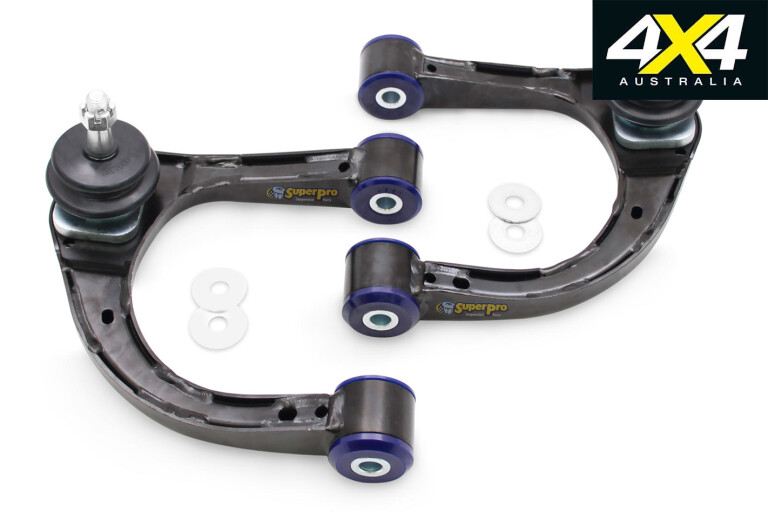
The twin-arm arrangement means there’s not only caster adjustment like a solid axle 4x4, but also camber to consider. Lifting an independent 4x4 even minimally can knock all these alignments out of spec and cause issues with ball-joint operating angles, clearance on both tyres, as well as other suspension components.
Aftermarket upper control arms are designed to alleviate all these issues, getting the suspension geometry and alignment back to factory or better.
David Atherton from SuperPro explains: “Generally IFS 4WDs come out of the factory with two degrees of adjustment, for every inch you lift your vehicle you will lose one degree of adjustment. This means that if you lift your 4WD and then go to get a wheel alignment there will be no adjustment to accurately align your vehicle. Adding an adjustable upper control arm gives back those two degrees of adjustment, allowing our 4WD to once again get an accurate alignment.”
Troy Schipper from Roadsafe adds another point often overlooked: “When the manufacturer gives a wheel alignment specification, it’s without raised height or increased tyre size. Larger tyres absorb caster, forcing you to run higher caster than stock to retain the same feel.”
Legalities
While Australian Design Rules are a fantastic implement to ensure the car next to you isn’t running plywood suspension arms, the channels for modifications are often murky and fraught with danger.
There’s been many people forced to uninstall better handling suspension or better performing brake upgrades because the owner didn’t tick the right boxes. Before a set of control arms can be fitted to your 4x4 they need to be proven to meet or exceed ADRs and OEM (Original Equipment Manufacturer) specifications. There are two ways this can be done.
The first is through the manufacturer itself. If they’ve gone through the process to prove their arms meet or exceed the factory specifications they’ll be able to provide you with the relevant paperwork.
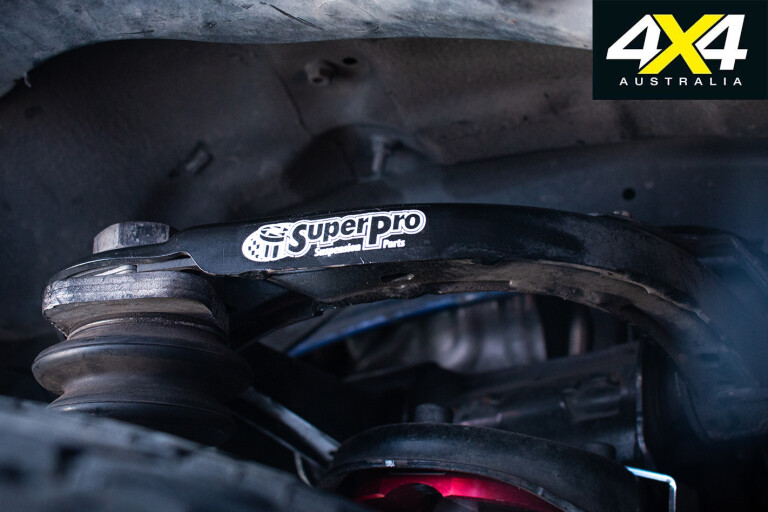
“National Code of Practice classifies these as a direct replacement component,” said Michael Hayes from Superior Engineering. In most states this should mean no further paperwork is required; although, if you do require engineering in your state it’s as simple as supplying the paperwork so no further testing is required.
If the manufacturer hasn’t jumped through these hoops it means the arms in their current state aren’t legal for road use, no matter how well (or poorly) they’re built. You’ll need to consult with an engineer and likely spend thousands in destructive testing to ensure they’re up to spec.
If the manufacturer can’t provide relevant paperwork you may as well have got the pizza delivery boy to weld them, as far as the law is concerned.
ADR compliance
So what exactly is involved in bringing a set of control arms to market, and why can’t your neighbour run a tape measure over a home-brew set and call them ADR compliant?
“Aftermarket arms are only legal if all components meet or exceed OE,” said Michael Hayes. “Some brands sold in Australia don’t have the correct ball-joint working angles. If a product is deemed road legal then it must in all aspects match or outperform the factory component; although, it can be vague when it comes to longevity of replaceable parts like bushes, bearings or other consumable items.”
To prove their components are up to scratch, high-end brands will often spend tens of thousands in testing, prototypes and computer modelling. This not only proves they’re not going to fall to pieces after pounding out hundreds of kays of corrugations, but also that they’re able to improve handling over the factory components.
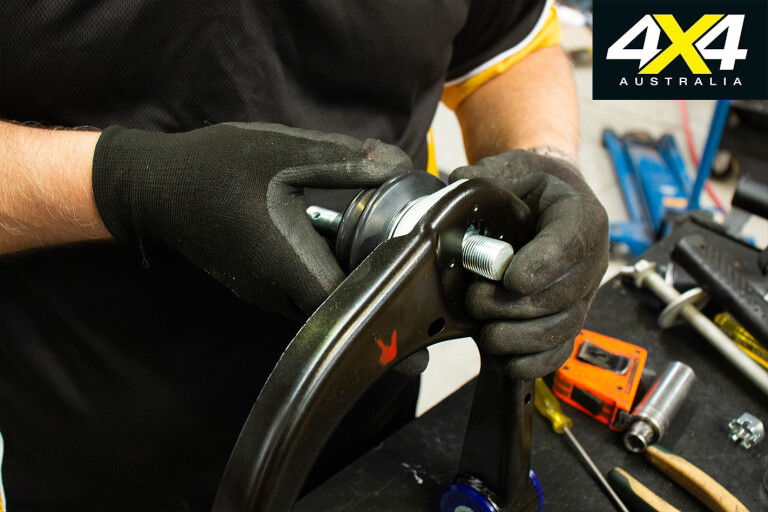
Unfortunately, nothing in life is that simple, and while your shiny new set of control arms might have the relevant paperwork, that’s not as important as who you’re actually buying them from.
“Unfortunately in Australia anyone can sell an arm,” says Cal Goodman. “We’ve seen many copies coming in from China and sold at very low prices.”
A widely known secret is the importation of direct copies of Australian products, often including manufacturer logos and ADR stickers without any of the appropriate testing or approval. While they might look identical, imported copies can run knock-off bearings, bushes and weak materials throughout their construction.
If you’re buying a set of arms from someone’s boot in a carpark, you might not be buying genuine components.
What to look for?
Even in the high-end segment different control arms have been designed with different uses in mind, so you’ll need to decide which product is right for you, not just for your Instagram followers.
ADR compliance and like-to-like fitment are the obvious requirements across any-use cases. It not only means it’ll be legal to run on your 4x4, but also that you won’t need to get the gas-axe out to fit them, reaming spindles to accept different pitch ball-joints or remaking suspension mounts to get an extra 5mm of wheel travel.
Additional mods
While redesigned upper control arms are part of a larger suspension system, they don’t typically require additional modifications to work.
“There’s no reason to run things like ball-joint spacers,” said Troy Schipper. “We rotate the ball-joint cup in the arm to maximise down travel.”
Michael Hayes added: “Ball-joint spacers or extended ball-joints also place additional loads on the weak factory arms and can cause cracking.”
With aftermarket control arms coming into their own with any lifts over 40mm they’ll typically be recommended in conjunction with diff drops, but they’re separate products solving separate issues. The diff drop helps correct CV angles, essentially adding strength to the front end. Control arms upgrade the factory’s weak arms and provide more clearance and better handling. Two sides to the same coin.
Improved off-road performance
Aftermarket control arms sound fantastic, don’t they? And they really are. They solve a lot of alignment issues, add strength back into a system pushed to its limits, and make your tyres last longer.
If that’s not enough, they can also increase off-road performance. So how do they give better off-road performance? By fixing a problem you’ve created.
As your suspension is lifted, the upper control arm becoming angled causes more issues than just your alignment. The first is binding of the upper ball-joint. It locks up with too much angle limiting down travel and wearing prematurely.
Likewise, the upper control arm wrapping around the strut means, with too much angle, it’ll also foul. By re-angling or redesigning ball-joints, as well as making more clearance around the strut tower and the tyre, redesigned control arms give more wheel travel, meaning your 4x4 has tyres on the ground for longer and there’s less chance of losing traction.
While there are legal minefields around both buying and installing control arms, reputable manufacturers make it a smooth affair and can make your lifted 4x4 perform better off-road and handle better on-road.
It’s no wonder they’re becoming more and more prevalent in complete suspension kits.
*This article was originally published in April, 2018
COMMENTS