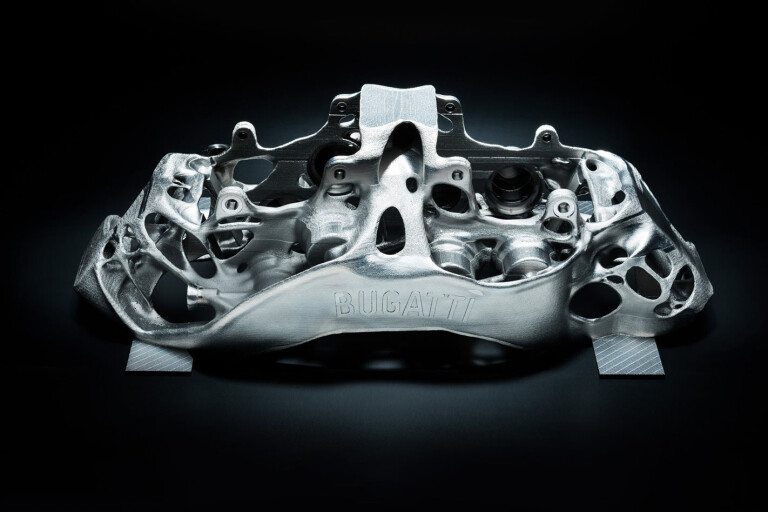
BUGATTI already has the most powerful braking system in the world fitted to its Chiron hypercar, but now the French company has gone a step further and started 3D printing enormous monobloc calipers.
The eight-piston caliper is claimed to be the largest functional car part that’s ever been 3D printed with titanium.
This achievement has seen Bugatti partner with Laser Zentrum Nord of Hamburg, and has seen Bugatti become the technical centre of excellence for 3D printing within the Volkswagen Group. Vehicle trials for the use of the caliper in series production are to start in the first half of the year.
“Vehicle development is a never-ending process. This is particularly true at Bugatti,” says Frank Götzke, Head of New Technologies in the Technical Development Department of Bugatti Automobiles S.A.S. “In our continuing development efforts, we are always considering how new materials and processes can be used to make our current model even better and how future vehicles of our brand could be designed.”
“As our performance data are often at the physical limits, we are especially demanding,” said Götzke. “This is why Bugatti always goes at least one step further than other manufacturers in the development of technical solutions.” That and the fact that Bugatti customers are probably a little less price sensitive than most when it comes to absorbing the cost of the expensive material.
Whereas the current Chiron uses an aluminium alloy for its calipers with titanium pistons, these development items are printed using aerospace-grade Ti6AI4V titanium. This material is used in the undercarriage or wing components of aircraft and rocket engines. The reason? It’s so much stronger than aluminium that titanium has been a troublesome metal to work in a traditional milling process.
It’s lighter too. The caliper, which is 41cm long, 21cm wide and 13.6cm high, weighs only 2.9 kg, which compares to 4.9kg for the aluminium component. Increasing strength while reducing unsprung component weight by 40 percent at each corner is a technical achievement that has Molsheim’s development team very excited.
It takes 45 hours to print each brake caliper, laying down 2213 layers of laser-melted titanium powder. The part is then furnace-treated at 700°C, falling to 100°C in order to eliminate residual stress and to ensure dimensional stability. The component is then removed, separated from its supporting structure and the rough edges smoothed away.
The final stage is to precision machine the functional surfaces on a five-axis milling machine which takes another 11 hours. At this point you probably understand why this process hasn’t been done before. Aside from the technological challenges, it’s incredibly labour-intensive and costly.
“It was a very moving moment for the team when we held our first titanium brake caliper from the 3D printer in our hands,” says Götzke. Bugatti isn’t stopping there though. “We have not only developed the world’s largest titanium component produced by additive manufacturing but also the longest aluminium component to date made by 3D printing,” Götzke explains, displaying a 63-centimetre-long lightweight aluminium windscreen wiper board. Tipping the scales at 0.4kg (half the weight of a die-cast item) it’s clear that Bugatti has only scratched the surface of what’s possible.
COMMENTS