THERE’S no RAA in Oodnadatta, no RACV halfway up Billy Goat’s Bluff, and you’ve got another thing coming if you try and call the RACQ with a flat tyre at the bottom of Gunshot.
It’s this reason we bang on about self-reliance and maintaining a well-stocked tool kit like a deranged bearded man preaches the end is nigh. And while the deranged bearded man might not hit the mark, you can bet your bottom dollar having the knowledge to get out of trouble – and the tools to do it – has saved more than a few lives on outback adventures.
This month we’re taking a look at one of the most under-rated pieces of equipment in any off-roaders kit: the jack. Now it’s easy to get excited over the latest laser-guided pneumatically operated mega jack, but unless you’re prepping your Prado to take on the Baja 1000 tools like that are often not the right tool for the job and will seriously eat into the fuel funds.
Here we’ll be looking at the pros and cons of the most typical jacks you’ll find in any 4×4, from high-lifts and exhaust jacks through to the stock one under your back seat right now.
OEM OEM (Original Equipment Manufacturer) jacks are often the first things people bin when buying a new 4×4. They’re seen as underpowered, undersized and of little benefit when you start installing suspension lifts and larger tyres. They often come in two varieties: screw-type or scissor jacks.
Scissor jacks earn their ridicule for low safe working loads (SWL), flimsy construction and low lift height, but screw jacks are undeserving of the hate. They’re simple in operation, with a pinion gear running against a crown wheel much like a diff. As the pinion and crown wheel spin they spin a worm gear, which pushes the lifting plate up or pulls it down.
The benefits of a jack like this are that there’s very little that can go wrong with them, and almost nothing that could cause instant failure under normal operation. Due to being able to run one worm gear inside of another they also have a surprising amount of lift for such a small package – our one tested having 230mm of lift for a maximum extended height of 420mm. Even with 35in tyres a Cruiser or Patrol’s axle tubes will be a maximum height of around 400mm, so the stock jack with a 50mm-thick timber base plate will still lift enough to change a tyre.
Unfortunately, life isn’t all sunshine and roses. Screw jacks often have limited lifting capacity under 2000kg, and depending on how heavy your 4×4 is lifting one end off the ground can overload the jack. However, they’re useful for lifting a wheel off the ground to change a tyre, or as a press to replace bearings in the field.
BOTTLE JACKS OFTEN seen as an upgrade to the screw jack, hydraulic bottle jacks are one of the most common jacks you’ll see. They’re available in multiple SWLs, from as little as 2000kg right through to 20,000kg; although, unless you’re planning on balancing five fully loaded 4x4s on the one jack, those weights may be overkill.
Much like a screw jack, hydraulic bottle jacks are incredibly compact, often occupying the spot the OEM screw jack came in. Rather than a series of gears inside, a bottle jack works by pumping hydraulic fluid from the storage container (the large bottle-shaped part) into the chamber underneath the jack’s ram. The benefit of this over a screw jack is the huge mechanical advantage you get, making it easier to move heavy loads.
The downside is that due to their design they aren’t able to lift as high as a screw jack. Despite having a larger capacity (10T) our bottle jack had a maximum lift height of 480mm with only 140mm of available travel, and a further 80mm in the screw top adjuster. They’re also considerably heavier than a screw-type jack and are more difficult to lower due to requiring the pressure release valve to be cracked, rather than a second pump to pump it out. Careful attention should also be paid to not damaging the seals.
Bottle jacks provide a larger lifting force over a smaller distance, and they’re available in many sizes. Some can be optioned with angled V mounts to more securely grab an axle tube; although, that will remove their ability to be used as a press. They’ll serve as a suitable replacement to an OEM jack, but whether or not they’re an upgrade is up for debate.
TROLLEY JACKS WHEN it comes to heavy lifting, trolley jacks are often seen as the go-to option. Much like a bottle jack they work by pumping hydraulic fluid from one compartment to another. Ironically enough, most trolley jacks require a bottle jack hidden underneath the main arm to do the lifting.
Trolley jacks are undoubtedly easier to use on flat ground than either bottle or screw jacks. They trade lifting capacity for speed and can have a wheel jacked up and back down before a bottle or screw jack could even reach the axle tube to start jacking.
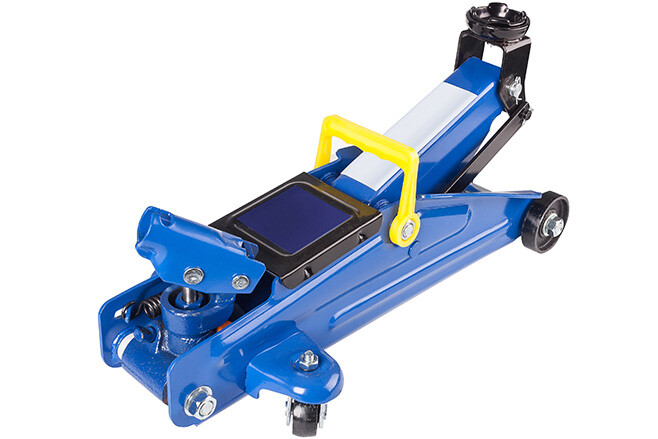
Lifting capacities range from 1400kg to 3000kg, and a longer reach allows you to position the jack underneath the 4×4 without having to get under there yourself. Due to their large base they’re also far more stable than most other options.
On the downside they’re incredibly bulky and heavy, taking up considerable storage space and eating into your GVM. They offer around 300mm of lift, which isn’t much when they start from as low as 130mm, but 300mm is plenty when fitted with an extension; although, due to the arc they operate on, the jack will need to roll freely underneath to keep the 4×4 centred, which can be difficult in rough terrain. Some off-road-specific versions are becoming commercially available, and they offer skid plates to prevent them sinking in soft terrain and have had their weight cut down to 20kg.
If you’re planning on doing a lot of lifting and don’t want to swing off a jack handle for 20 minutes, then a trolley jack is a great option, but you trade a lot of benefits for speed.
HIGH-LIFTS THE ubiquitous high-lift jack is almost a fashion choice for many off-roaders, being firmly attached to rear bars and roof racks with often very little understanding of why it’s even there.
Unlike the previous jacks, a high-lift works more like a ladder. The spine has holes along its centre which allow the pins, or feet, of the lifting mechanism to walk their way up. With a long handle and very little distance between holes, the mechanical advantage is huge. They’re generally rated over 2000kg and offer lifting heights unheard of in any other type of jack. They can also be used in a variety of other roles such as a homemade press, tyre-bead breaker, or even a make-shift winch if the $50 special and free stubby cooler leaves you in the lurch.
The downside is they’re incredibly unstable, and the jack handle has bested more than a few jaw bones over the years. They’re also tall and won’t fit under the vehicle, so can’t be used to jack an axle tube up, instead relying on slings or limiting straps to get the job done.
They’ve become part of the overlander uniform and it’s not without reason, they just shouldn’t be the go-to tool if you need to change a tyre or work on your brakes. Think of them as part of your recovery kit rather than a jack and you’ll have years of success.
EXHAUST JACKS EXHAUST jacks can be completely useless in one tool kit, and a god-send in another. Their design and operation is incredibly simple: a heavy-duty bag that’s taller than it is wide slips underneath the 4×4, while a connection hose slips over the exhaust tip. As the exhaust gases fill the bag it pushes upwards, lifting your 4×4 off the ground.
They’re lightweight and pack flat, making them easy to store behind seats, down the side of drawers or anywhere else that’s usually dead space. They also have the largest base of all the jacks and are able to easily conform to uneven terrain, making them perfect in soft sand. Their low profile also means you can easily slide them under bogged vehicles.
They offer around 750mm of lift, which is huge if you’re bogged but not a great deal if you’re attempting to raise a lifted 4×4 off the rock sliders. They’re also rated up to around 4000kg, but aren’t recommended for lifting underneath axles or any sharp or hot objects. On the downside they are vulnerable to damage, aren’t easy to control up or down, and have a very narrow range of uses.
If you’re constantly travelling on sand they can be an absolute life-saver. On rocky or reasonably firm terrain they’ll rarely be the best option.
FIVE RULES TO WORKING ON A RAISED 4X4 1: A STABLE BASE Unless you’re lifting a can of coke with a trolley jack, chances are you’ll be putting a significant amount of weight onto a concentrated point. High-lifts, bottle jacks and screw jacks all benefit from a base when lifting on anything other than hard-packed dirt. They can also provide a more stable platform that prevents the jack from slipping.2: THE RIGHT JACK Don’t use a high-lift when a bottle jack will do, don’t use a bottle jack when you need a high-lift, and don’t use an exhaust jack if you’re planning on getting under it.
3: DON’T BE A PANCAKE Stop and think about what you’re doing. In even the most routine jacking operation you’re lifting a tonne or two into the air and balancing it on one shaft. What will happen if it comes off? Axle stands and a set of wheel chocks are an absolute must in any situation. If you’re out bush then at least throw the spare tyre underneath.
4: KEEP IT LOW The higher you lift something, the less stable it’ll be. Not just because the 4×4 is higher, but because jacks become less stable the higher they’re wound up. It amplifies any movement at the bottom and can quickly push the 4×4 off the jack.
5: PREDICT THE FUTURE When you lift a 4×4 you change its centre of gravity, what’s holding it in place, and how stable it is. Think about what you’ll do and what effect it will have on the rest of the 4×4. Will turning the wheel you’ve just lifted off the ground force one of the fronts to turn, rolling you off the jack? Will jacking it up in the first place send it careening downhill, warranting connecting the winch line before you lift it? If you’re on your own changing a tyre you’ll still be on your own if you roll your 4×4 or break your tools. so use your noggin.