The clue is in the name. A shock absorber ‘absorbs’ the shock transferred from bumps and dampens the forces a vehicle is subjected to, by controlling the dissipation of energy within a vehicle’s suspension – regulating the springs’ energy using friction and resistance. Put simply, this is achieved by converting kinetic energy caused by the shock into another form of energy – heat – which is then dissipated.
“Whilst it is the job of the spring to support the weight of the vehicle, it is up to the shock absorber to control the stored energy of the spring, the vehicle body motions and the sprung and unsprung weight of the vehicle,” Ben Dobinson from Dobinsons Springs explained.
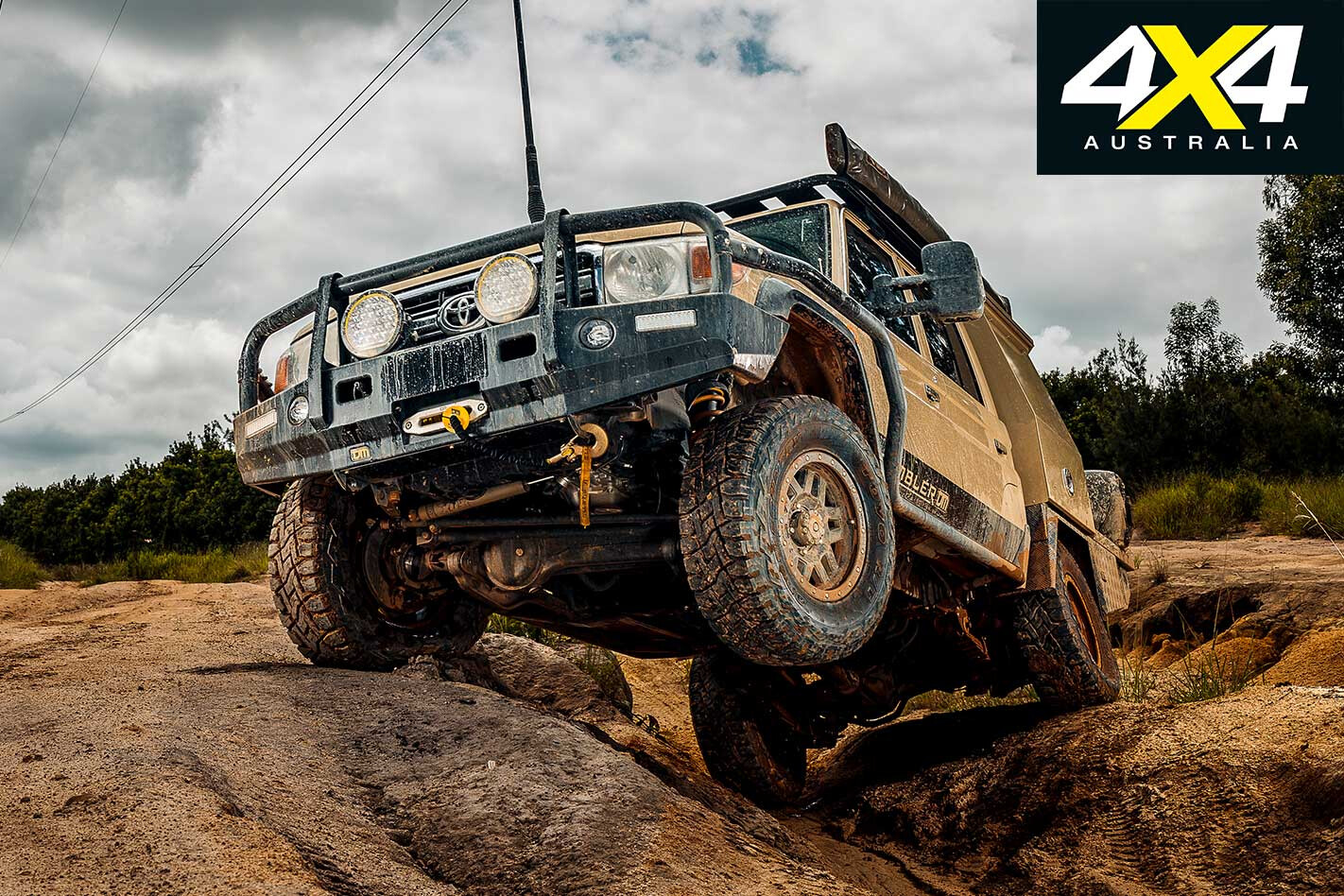
“A shock absorber works by restricting oil through an orifice, usually a piston and shim assembly, to provide a damping force which transfers kinetic energy into heat.”
Ironman 4×4’s Kristian Ristell added that the amount of damping is critical and carefully set by the manufacturer, ensuring body movement is controlled to minimise unnecessary movement. As well as tyres maintaining contact with the road.
“Energy cannot be created or destroyed, but only transferred,” Tough Dog’s David Cook explained. “In this case the movement of the spring which is kinetic energy is transferred into heat energy through the shock’s resistance, which is then dissipated through the oil of the shock. This is why shocks get hot as you use them in harsh conditions, because there is more energy that needs to be dissipated.”
An off-road shock needs to be more robust to handle the challenging conditions of both arduous tracks and long outback roads, and therefore capable of withstanding the incredible amount of heat that’s generated.
“A shock absorber is a critical part of your vehicle’s control components and its effective operation is integral to the safe operation of your vehicle,” Adam Gillick from Pedders Suspension told us.
Types of 4×4 shock absorbers
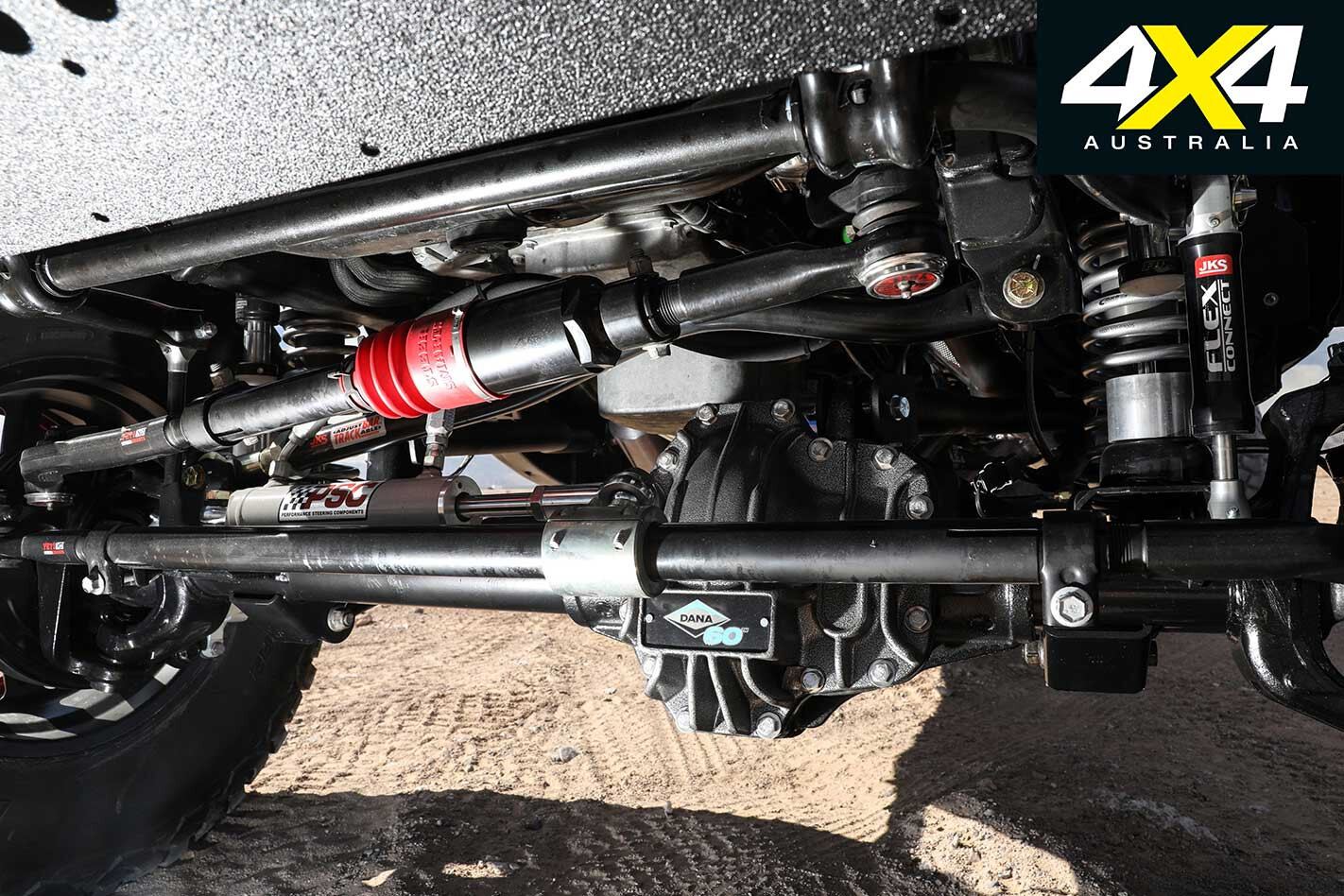
Generally there are two types of conventional shock absorbers: twin-tube and monotube. Monotube shocks have one tube (obviously) and the piston runs up and down through the oil; with a twin-tube shock, one tube is positioned within the second tube (like a babushka doll, as David Cook put it).
“As the shock moves up and down, the oil inside flows through the piston and the foot valve, which transfers oil from the inner tube (or working tube) and the outer tube. This kind of acts like an oil reservoir, and also as an oil jacket, around the shock,” Cook said.
You’ll find twin-tube designs in most road-going passenger cars, utes and SUVs due to their comfortable on-road characteristics. Monotube shocks are typically used on performance-oriented vehicles, and are becoming more popular for 4×4 vehicles – particularly for on-road use.
There are then variants within twin-tube and monotube designs such as nitro-gas charged, foam cell twin tubes, single body internal floating piston monotubes, and remote reservoir shocks which move the additional oil capacity out to a separate canister mounted near the shock and connected by an oil line.
“There are then additional features such as adjustable damping and position-sensitive damping that can also be built into shock absorbers,” Ben Dobinson added.
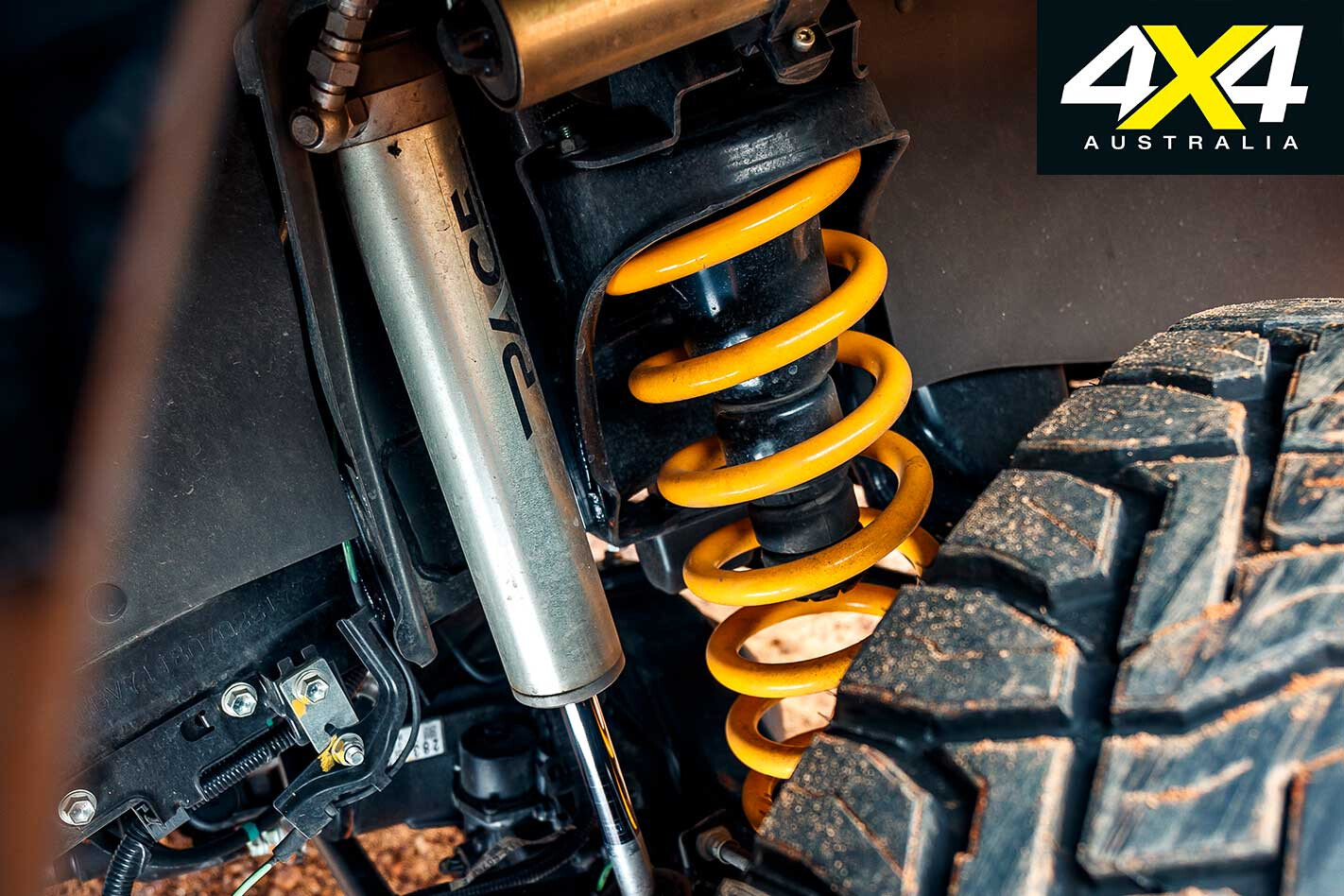
Monotube shocks do have a number of drawbacks for off-road environments, as Ironman 4×4’s Kristian Ristell explained: “(They are) vulnerable to impact damage, and high gas pressurisation can lead to a higher risk of leaking and lower oil volume which can cause overheating.”
Twin-tube shocks, on the other hand, are more protected from the elements. “Twin-tube shocks are naturally resistant to damage from rocks and debris due to a second layer of ‘armour’ which protects the piston tube,” Ristell said. “Lower gas pressurisation also means they are less prone to leaking and can have a longer service life.
“Twin tube shocks in general are a more reliable and trouble-free concept for off-roading due to their strong style of construction,” he added. “Monotube shocks are well-suited to on-road environments where high precision or tuning is required. In some cases they can also be more vulnerable to damage or leaking in an off-road environment.”
When it comes to finding a shock absorber more suited to the bumps and grinds of serious four-wheel driving, though, it’s important to ensure your suspension componentry ticks all the boxes for your 4×4’s intended purpose.
“You wouldn’t buy an X-Trail as a hardcore off-road tourer, so you wouldn’t buy shocks that aren’t up to the task either,” said Tough Dog’s David Cook.
Why go to the aftermarket?
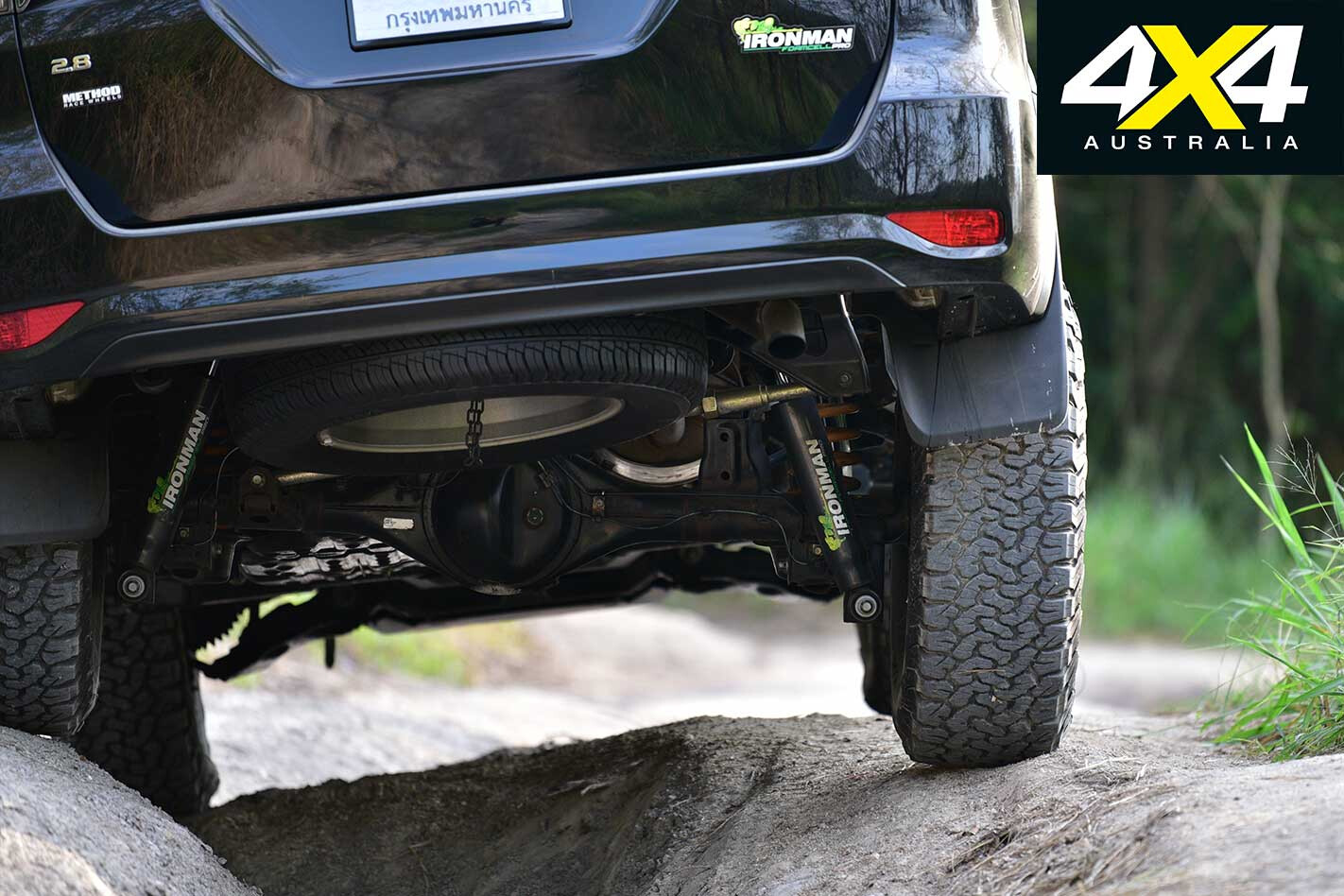
OEM units are built to a cost – and within bureaucratic parameters – and will be capable enough for most people who don’t depart the grid in search of the old black stump. Manufacturers typically cater for the broader population – which makes sense – but that means the equipment will often be lacking for specific requirements.
For the 4×4 crowd the aftermarket is where to turn to ensure you are set up properly for remote travel, hardcore off-roading, or whatever floats your boat, as the industry has a lot more freedom to target specific uses – towing heavy loads, for example.
“The aftermarket generally does away with all the bureaucracy and focuses attention to providing targeted solutions aimed at real-world customer use,” Ironman 4×4’s Kristian Ristell said.
Upgrading your 4×4 with aftermarket gear often leads to a domino effect, and it’s no different for shock absorbers. Installing a lift kit? You’ll need shocks to suit.
“Think of it this way,” Tough Dog’s David Cook explained, “if you beef up the spring or lift the vehicle, you need a shock that is a fair match for that spring, otherwise you have a Pee-Wee Herman-sized shock in the ring with a Mike Tyson-sized spring. If you’ve changed the height of the vehicle with a lift kit, then the corresponding shock will also be longer to accommodate that.”
Ben Dobinson agreed: “As soon as you are looking to raise the vehicle, carry constant loads or look to spend a little more time off the bitumen then the OEM shock absorbers are too short, do not have sufficient damping and are simply just too small to do the job. This is where a good quality aftermarket shock steps in to meet the demands of Australian 4x4ers.”
Off-Road maintenance
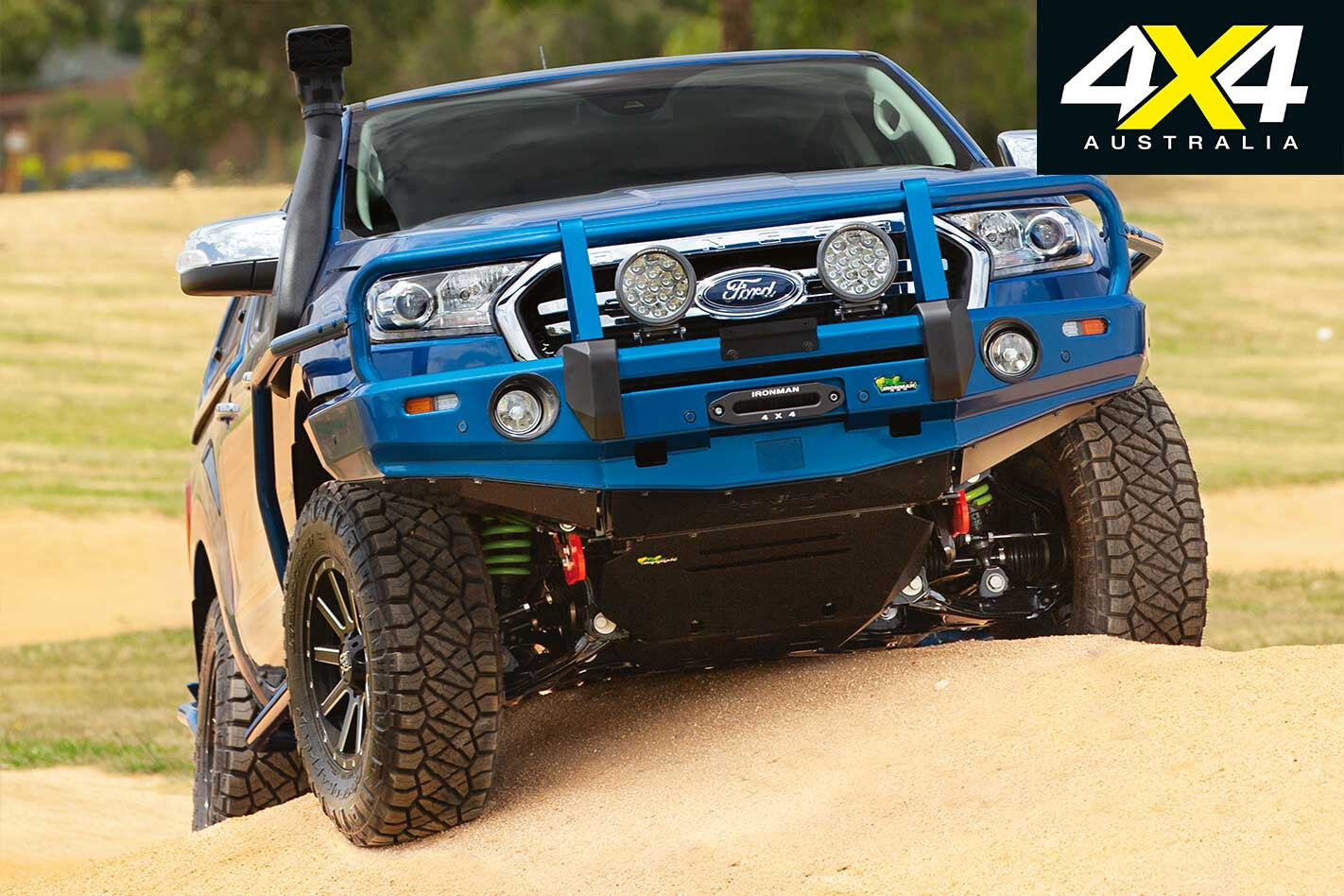
All of the experts agreed that if you make smart decisions at installation, it’ll save you from a world of hurt down the track… literally. Buy a quality product from a reputable brand, and a shock absorber that suits the kind of driving you have planned, and you’ll be laughing on your camp chair in the middle of nowhere.
“There is no point buying the most expensive, flashy racing shock for a vehicle that is going to circumnavigate the continent,” Tough Dog’s David Cook said. “They are designed for high performance but not necessarily stamina.”
It’s also important to ensure the vehicle is set up correctly: “Ensuring the vehicle is set up correctly and the shock absorbers are not being bottomed out or damaged is the most important factor,” Ben Dobinson told us. “From there it’s just a matter of keeping the shocks clean and clearing out any accumulated debris from the seal area as soon as possible.”
Kristian from Ironman 4×4 reiterated that point: “Any quality suspension installer should always only tighten shock absorber bushes at ride height, especially lower strut bushes. This is referred to as ‘neutralising the bushes’ and it ensures the bush remains relaxed at ride height to maximise bush life. If the bush is tightened with the wheels hanging, the bush is twisted and is subjected to more torsional stress resulting in shortened life.”
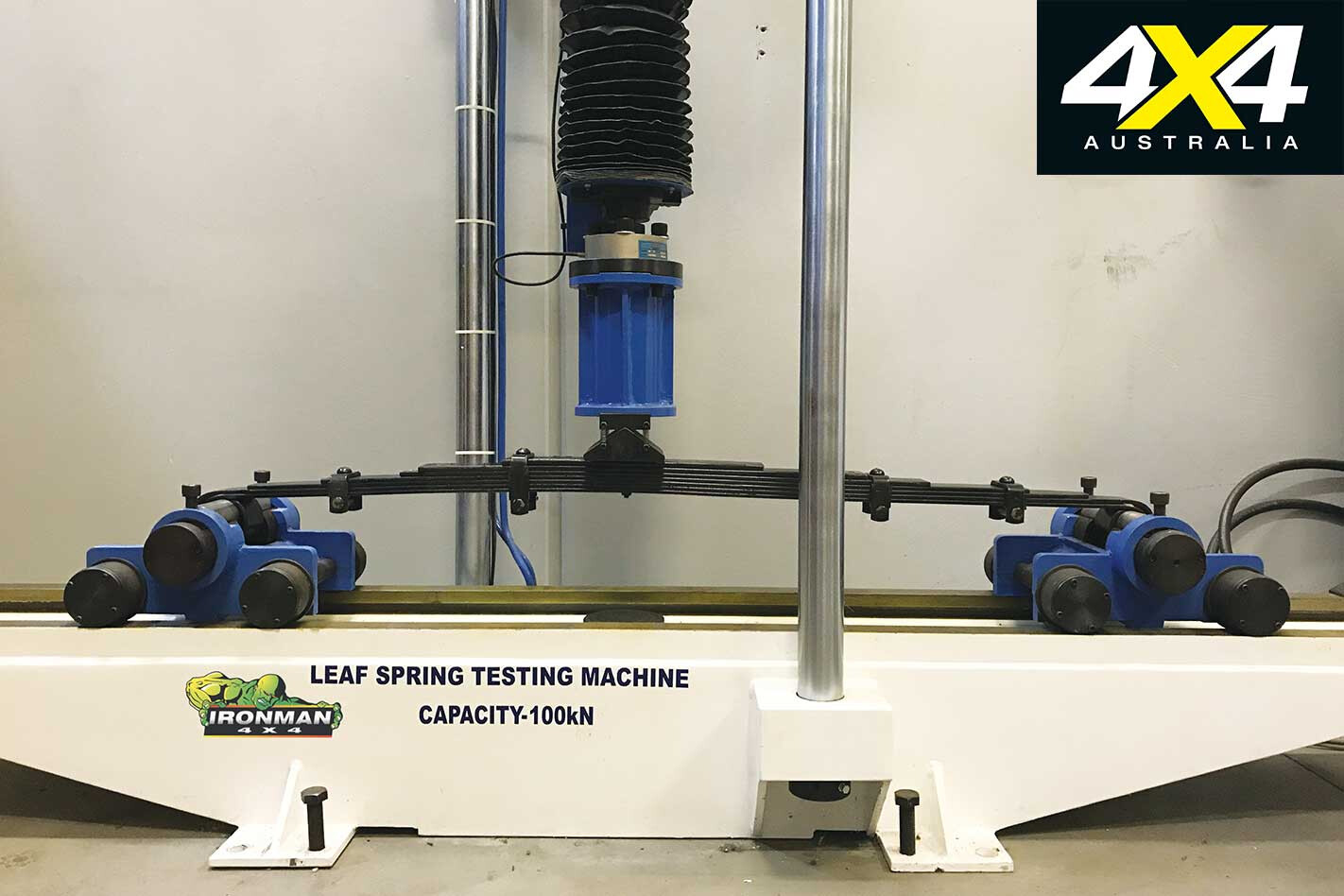
Overheating – especially in rough off-road terrain – could shorten the lifespan of a shock absorber, so that’s why it’s vital to always get the correct shock for your intended purpose. For example, a small body gas-pressurised shock can overheat quickly due to its relatively small oil volume and surface area; while larger bodied shocks – like Ironman 4×4’s Foam Cell Pro shock absorbers – have a higher oil volume and larger surface area than gas-charged shocks.
“This means they are effectively a larger radiator, expelling more heat in a shorter amount of time,” Ristell said. “Meaning you can drive for longer in those arduous outback conditions before shock fade sets in.”
“Ensuring all of the components of a vehicle’s suspension system are working is also important, as worn equipment – springs or bushes – could put shock absorbers under undue stress,” explained Adam Gillick from Pedders. To remedy this he recommends punters have brake and suspension checks at least once a year.
Worn out?
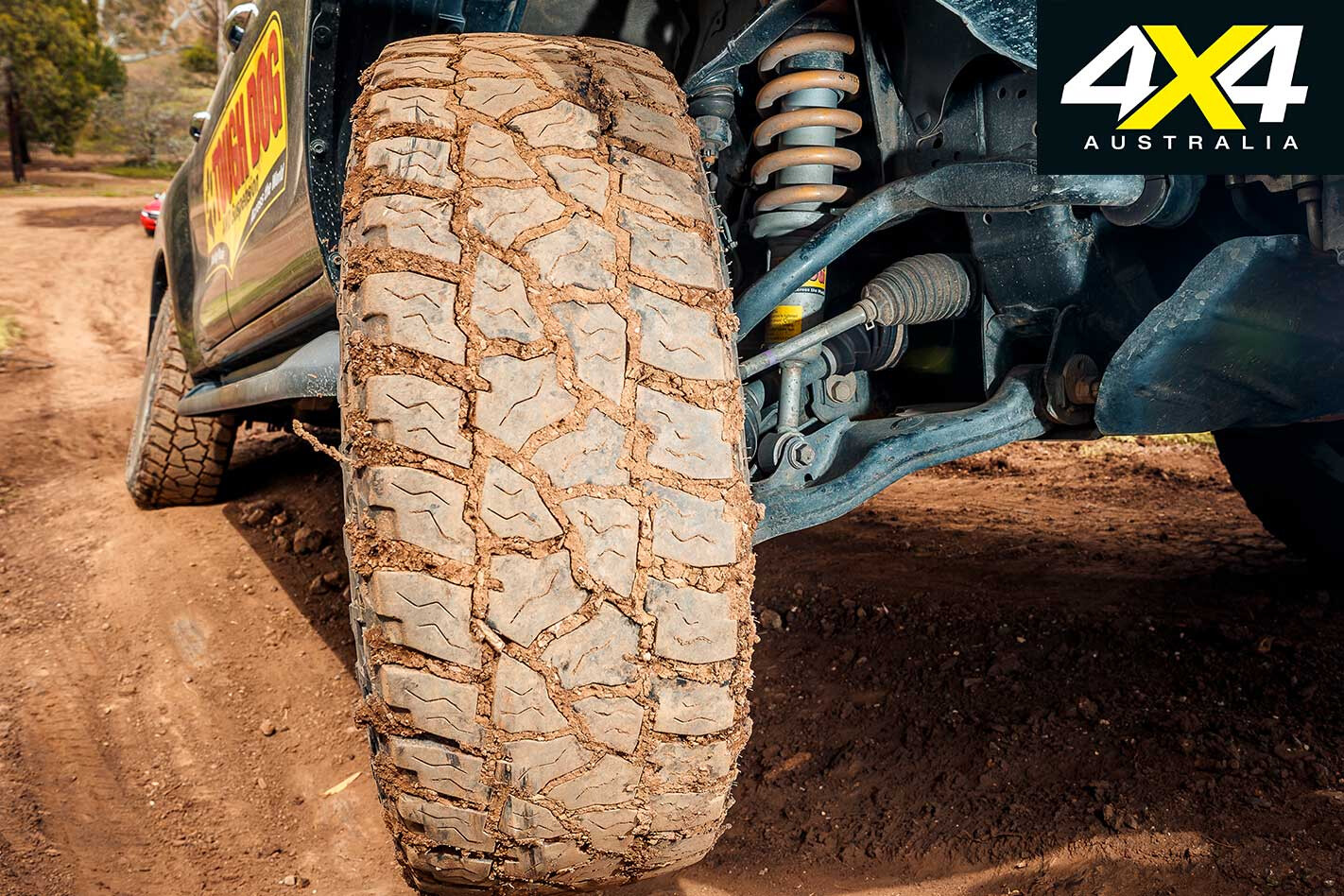
How do you know when it’s time to replace your shock absorbers? It’s inevitable that a shock absorber will eventually wear out over time, just like any mechanical part that’s constantly abused. The first and most obvious sign that it might be time to replace a shock is that your 4×4 won’t ride as smoothly as it should.
“When driving, worn shocks may cause an unsettled ride, crashing over bumps as the shock piston is unable to keep up with the frequency of bumps in the road surface,” Pedders’ Gillick explained.
“Increased braking distance is also a warning sign. Add to this excessive tyre wear and poor alignment.”
Tough Dog’s David Cook affirmed that point: “If the vehicle is recycling or bouncing more than once after travelling over a large bump, then the shock is probably due for replacement. Essentially, when there is a noticeable drop in the shock’s ability to control the energy of the spring, then they will need a seeing to.”
Losing large amounts of oil is also a sign that something is amiss in your springs. Looking beneath your 4×4 will also reveal issues with your suspension, as Ben Dobinson explained: “Usually, any signs of obvious damage such as bent or heavily chipped shafts, (and) large dints in the shock body that may affect the working tube,” he said.
What happens over time?
“Precision tolerances within friction surfaces will very slowly become affected, shedding microscopic metal particles into the oil during its entire surface life, in much the same way an engine does,” Kristian Ristell from Ironman 4×4 explained. “The oil itself will also break down over many years reducing its viscosity and suffering due to the effects of heat and particle contamination.”
What to look for?
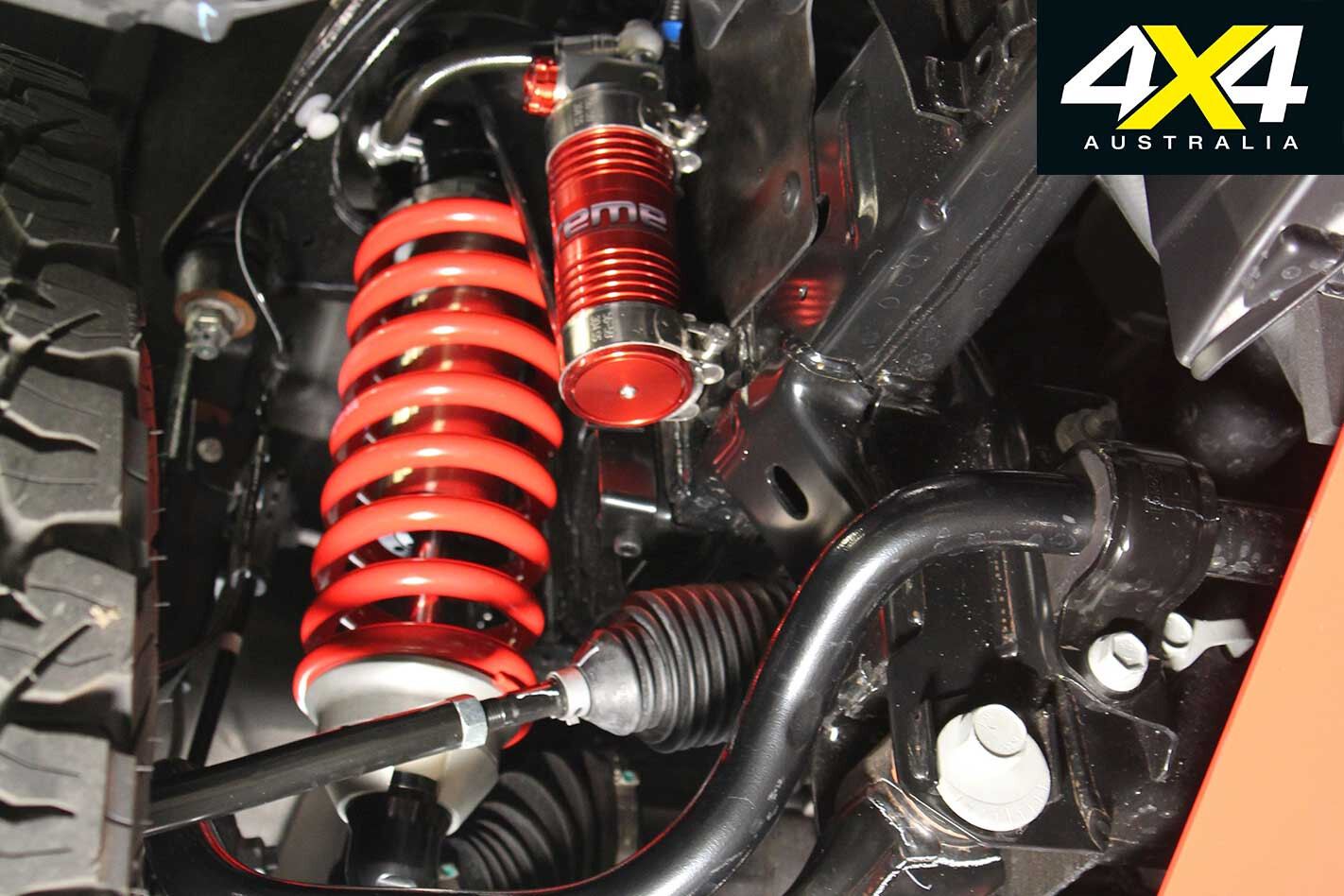
As mentioned, different shock absorbers are designed for different jobs, so what to look for ultimately comes down to your four-wheeling intentions. Rather than buying a ‘bad’ shock – as a bad shock will be found out pretty quickly and pulled from shelves – the biggest mistake is buying a shock that doesn’t suit your setup and/or your springs.
Still, you get what you pay for, as Ben Dobinson explained.
“A good quality shock will provide a far more comfortable, controlled ride consistently, with noticeable improvements in handling, reduced body roll and reduced bottoming out,” he said. “A poor quality shock will generally result in earlier failure, shock damping fade early on at low temperatures and a more uncontrolled ride.”
Having the wrong shock, or a shock of sub-par quality, can lead to a few issues including shorter lifespan of the shocks, bad ride quality and increased tyre wear.
“Poor quality shocks often use lower quality materials and mismatched valving which leads to shorter product life and poor ride characteristics. It’s worth taking the time to find a product that perfectly matches your vehicle and driving style and is backed by a solid warranty,” Adam Gillick from Pedders said.
“A good quality shock will have undergone the necessary R&D and material development to ensure that it will perform to its specification throughout its working life. In short – better ride, smoothness and long-term durability are key benefits of a good quality shock absorber,” he said.
Type of 4×4 shock absorbers
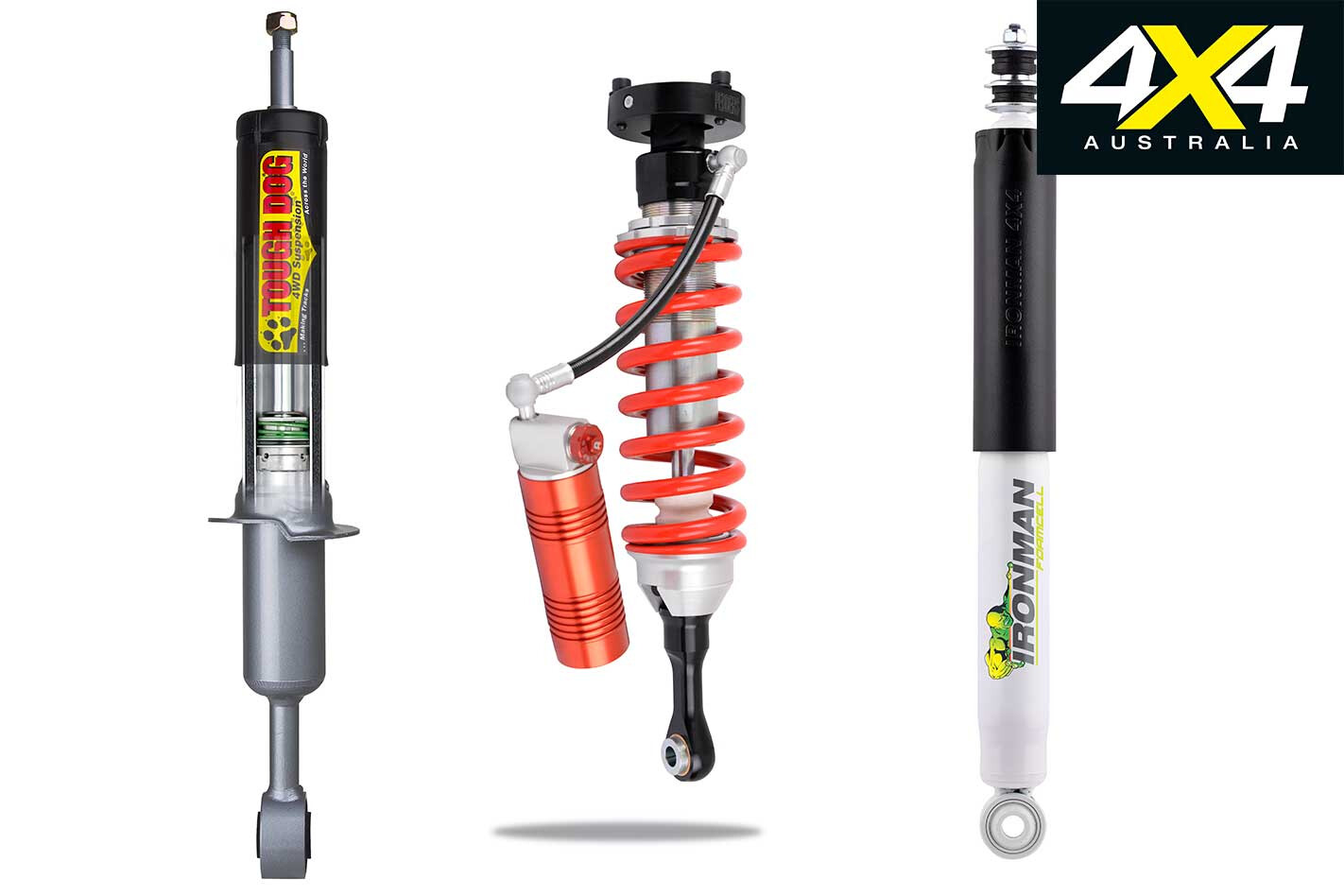
Coilover With a coilover shock absorber, the coil spring is integrated into the design of the shock absorber. “Coilovers are for customers who want the ultimate in performance and tuning ability, with compression and rebound damping, as well as ride height being adjustable,” Adam Gillick from Pedders said.
Gas-charged shocks Instead of using a foam sleeve like a foam cell shock absorber, a gas-charged shock uses a low-pressure charge of nitrogen gas. Gas-charged shocks are hugely popular in modern vehicles. “Small-bodied, twin-tube, gas-charged shocks are great value for everyday use. Hence why they are popular from the original vehicle manufacturer,” Kristian Ristell from Ironman 4×4 said.
Remote reservoir “Remote reservoir shocks can offer similar benefits than a large-bodied foam cell shock, since the intention is to increase oil volume; but this only works in long travel applications which cycle the fluid in and out of the reservoir, such as dedicated race vehicles,” Ironman 4×4’s Ristell said. “Modern vehicles with little wheel travel rarely benefit from a remote reservoir shock, as there is simply not enough fluid displacement to transfer the heat into the canister.”
Foam cell A foam cell shock is similar to a gas-charged shock in construction, the difference being use of a foam sleeve within the absorber instead of the gas charge. Ironman 4×4’s foam cell shock absorbers, for example, have the capacity to house more oil due to the sleeve occupying less space, enabling it to dissipate more heat.
For Tough Dog’s range of foam cell shocks, the foam cell piece is located between the inner and outer tubes and is injected with micro bubbles of nitrogen gas. In this way, the gas and the oil cannot mix, which means you avoid bubbles in the oil (aeration).
Pedders also offers foam cell shocks that are engineered to virtually eliminate shock fade, as the oil in the shock has full contact with both the inner and outer housings.
4×4 shock absorber manufacturing process
BEN Dobinson from Dobinsons Suspension walked us through the company’s manufacturing process:
“We start here in Australia by taking all the vehicle information such as dimensions, weights, spring rates and suspension geometry, as well as the vehicle type and market requirements. From there we calculate the required shock dimensions and damping requirements.
“From there the completed drawings are moved into pre-production samples which are tested here on shock dynos, shock destruction and fatigue testing machines, and then on vehicle testing.
“For monotube shock absorbers the manufacturing process starts with DOM seamless tubing cut to length and machined. From there the tubes are precision honed to +/- 0.04mm. The shock absorber body ends are CNC-machined to shape and then CNC Robotic TIG-welded to the shock absorber bodies. The high-flow pistons, Seal Head Assemblies and spring seat collars are CNC-machined from T6 6061 aluminium. The 5140 shafts are machined, heat-treated and then hard-chromed. All components are taken through a three-step ultrasonic cleaning process where the bodies are then EDP-coated before moving into assembly.
“The shock absorbers are assembled, filled with FUCHS oil and charged with nitrogen gas before they are dyno-tested to ensure that every shock meets the required damping performance. The shocks are then fully cleaned before hanging on an inspection rack for a few days to ensure no leaks occur before packaging.”